- Home
- BLOG
- Cylindrical Grinder
- Automated Match Grinding Solutions for Hydraulic Valve Components
Automated Match Grinding Solutions for Hydraulic Valve Components
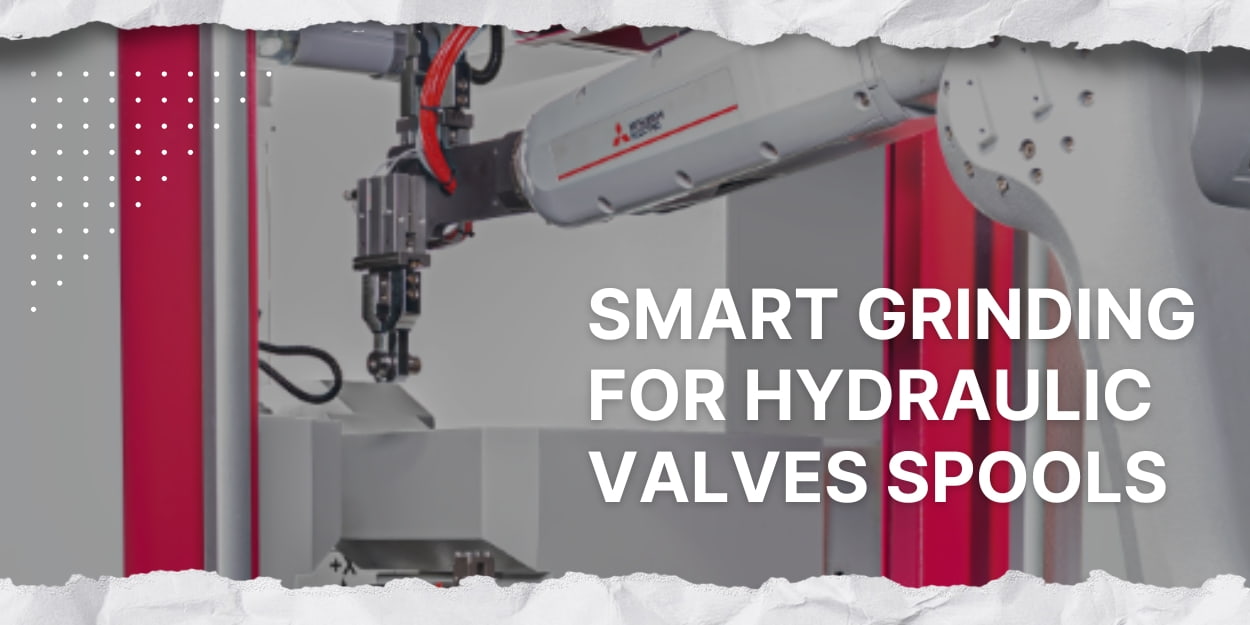
Precision grinding of hydraulic valves is crucial for their reliable operation across various industries. Whether in hydraulic and pneumatic systems, the automotive sector, or precision instruments, the perfect fit between the valve spool and body is essential for sealing and overall system performance. By leveraging advanced automated grinding technology, manufacturers can achieve higher precision and efficiency, ensuring every component meets the strictest quality standards.
Hydraulic systems use hydraulic oil as a medium to convert electrical or mechanical energy into pressure energy via hydraulic pumps, powering various machinery. To maintain stable operation, high-pressure hydraulic oil must be carefully regulated through multiple hydraulic components to control pressure and flow. Among these components, hydraulic valves play a critical role in ensuring system efficiency and performance.
Hydraulic Valve Spool Grinding Solution
Grinding Machine Selection Guide: Key Factors to Consider
In hydraulic parts manufacturing, precision grinding for hydraulic valve spools is a critical process to ensure sealing performance and system stability. The selection of the grinding machine depends on the material, tolerance requirements, and production volume of the valve spool.
■ Cylindrical Grinding Machines are ideal for valve spools with center holes, delivering high-precision outer diameter grinding with roundness and concentricity accuracy down to the micron level (μm).
■ Centerless Grinding Machines are best suited for high-volume production, offering efficient processing while maintaining consistent dimensional tolerances.
■ For valve spools with strict inner diameter and roundness tolerances — typically within just a few microns — Internal Grinding Machines provide the precision required to achieve high-accuracy bore dimensions and surface finishes.
By selecting the right grinding machine, manufacturers can optimize both production efficiency and component quality, meeting the stringent demands of hydraulic systems.
〈Extended reading:GRINDING MACHINE: essential for precision machining in manufacturing industry〉
The productivity of cylindrical grinding machines depends on various factors, including workpiece size, tolerance requirements, grinding wheel type, and the level of automation.
Compared to centerless grinding machines, cylindrical grinders typically offer slower processing speeds, making them more suitable for high-precision, small-batch, or multi-variety production. However, when equipped with an automatic loading and unloading system, cylindrical grinding machines can improve efficiency and meet medium-volume production demands.
For large-scale production, centerless grinding machines remain the more efficient option due to their faster processing capabilities and continuous feeding design.
The productivity of cylindrical grinding machines depends on several factors, including workpiece size, geometric accuracy requirements, grinding wheel type, and the degree of automation.
In general, cylindrical grinding machines operate at slower processing speeds compared to centerless grinding machines, making them ideal for high-precision, diverse, or assembly-part production. When integrated with an automatic loading and unloading system, cylindrical grinders can improve efficiency and meet medium-volume production demands.
However, for mass production, centerless grinding machines remain the more efficient option, offering faster processing speeds and continuous operation.
TOPKING Cylindrical Grinding Machine Models Reference
Recommended Cylindrical Grinding Machine Models
2NC Cylindrical Grinders:T-1012、T-1020
CNC Cylindrical Grinders:X-25、X-2540A(end face grinding)、X-2540LM
Recommended Centerless Grinding Machine Models
NC Centerless Grinder:H-4520-NC (thru-feed or in-feed grinding customization)
CNC Centerless Grinder:H-4520-CNC (thru-feed or in-feed grinding customization)
〈Extended reading:GRINDING MACHINE: Struggling with Inefficient Grinding Operations?〉
Hydraulic Valve Spool Grinding Solution | TOPKING Recommends X-2540LM
The TOPKING LM Series CNC Cylindrical Grinding Machines are equipped with a linear motor-driven cross slide, enhancing machine rigidity and stability. This advanced design significantly reduces processing time while meeting high-efficiency and high-precision grinding requirements.
The LM Series is especially suitable for hydraulic valve components, automotive parts, and aerospace components, ensuring exceptional precision and consistent production quality.
With improved performance and stability, the TOPKING LM Series provides the perfect solution for industries requiring high-precision grinding and efficient production processes.
CROSS-SLIDE
Unlike traditional grinding machines, the TOPKING X Series CNC Cylindrical Grinding Machines adopt a cross slide design for the X and Z axes. The grinding wheel head is mounted on the cross slide, enabling precise forward, backward, and lateral movements to accurately control the workpiece position during grinding.
In contrast, the worktable is fixed directly onto the machine base and does not move along with the grinding components. This innovative structure reduces the machine's footprint while enhancing grinding efficiency — making it especially suitable for production environments with limited space.
LINEAR MOTOR DRIVEN X-AXIS
The TOPKING LM Series CNC Cylindrical Grinding Machines feature a linear motor drive combined with high-precision linear guideways, eliminating mechanical friction and backlash during feed motion. The X-axis is equipped with a standard full closed-loop optical scale feedback system, ensuring precise infeed accuracy and dynamic response.
Compared to traditional ball screw systems, this design simplifies the mechanical structure, reduces the number of components, and improves space utilization — making the machine more stable, low-maintenance, and efficient.
The non-contact linear motor drive eliminates transmission gaps and mechanical wear, enhancing grinding consistency and extending machine lifespan — ensuring long-term, high-efficiency operation.
DUAL SYNCHRONOUS WORK SPINDLES
The LM Series offers an optional dual-drive workhead and tailstock with a dual-center synchronous drive system and an extendable spindle. This design simplifies workpiece clamping, reduces fixture complexity, and eliminates the need for additional drive considerations. The extendable spindle overcomes the travel limitations of the tailstock, allowing the equipment to quickly adapt to different workpiece lengths, minimizing tailstock adjustments during workpiece changes, enhancing processing flexibility, and meeting diverse manufacturing needs.
AUTOMATION APPLICATION
In the precision grinding process of hydraulic valve bodies and spools, the robotic arm automatically grips the valve body and performs inner diameter measurement with high precision. The measurement data is fed back to the controller in real time, enabling instant data processing and adaptive adjustment.
Next, the system automatically loads the valve spool and positions it in the grinding area. To ensure precise dimension control during grinding, the machine is equipped with advanced in-process outer diameter measurement technology. The linear motor drive precisely controls the infeed axis positioning, enabling real-time size monitoring and accurate adjustments, achieving high-precision grinding and intelligent matching for automated mass production.
The machine adopts a dual-driven spindle system, replacing the traditional tailstock adjustment method. This design significantly reduces workpiece loading, unloading, and changeover time, enhancing production efficiency and operational stability.
This fully automated grinding solution not only improves machining accuracy but also optimizes the production process, reduces maintenance costs, and ensures long-term stable performance — making it the ideal solution for high-precision mass production.
Smart Grinding Solutions for Hydraulic Valve Components
For manufacturers of high-precision hydraulic valve components, selecting the right grinding machine is crucial to ensuring consistent quality and production efficiency. Beyond meeting basic machining and accuracy requirements, stability, durability, and low maintenance costs are key factors in determining long-term performance.
TOPKING CNC grinding machines leverage advanced linear motor technology and high-precision measurement systems to deliver exceptional accuracy and long-term operational stability. This not only guarantees consistent machining quality but also helps reduce maintenance costs and maximize production efficiency — making TOPKING the ideal choice for businesses seeking to stay ahead in a competitive market.
Contact us today to learn how TOPKING grinding machines can optimize your hydraulic valve production — boosting both precision and efficiency!
Article Classification
Recent Articles
- How to Choose the Right CNC Grinder: Match the Control System and Machine to Your Production Needs
- Hydrostatic Technology: The Key to Stable Centerless Grinding
- Automated Match Grinding Solutions for Hydraulic Valve Components
- Struggling with Inefficient Grinding Operations?
- GRINDING MACHINE: essential for precision machining in manufacturing industry