- Home
- BLOG
- Centerless Grinder
- Hydrostatic Technology: The Key to Stable Centerless Grinding
Hydrostatic Technology: The Key to Stable Centerless Grinding
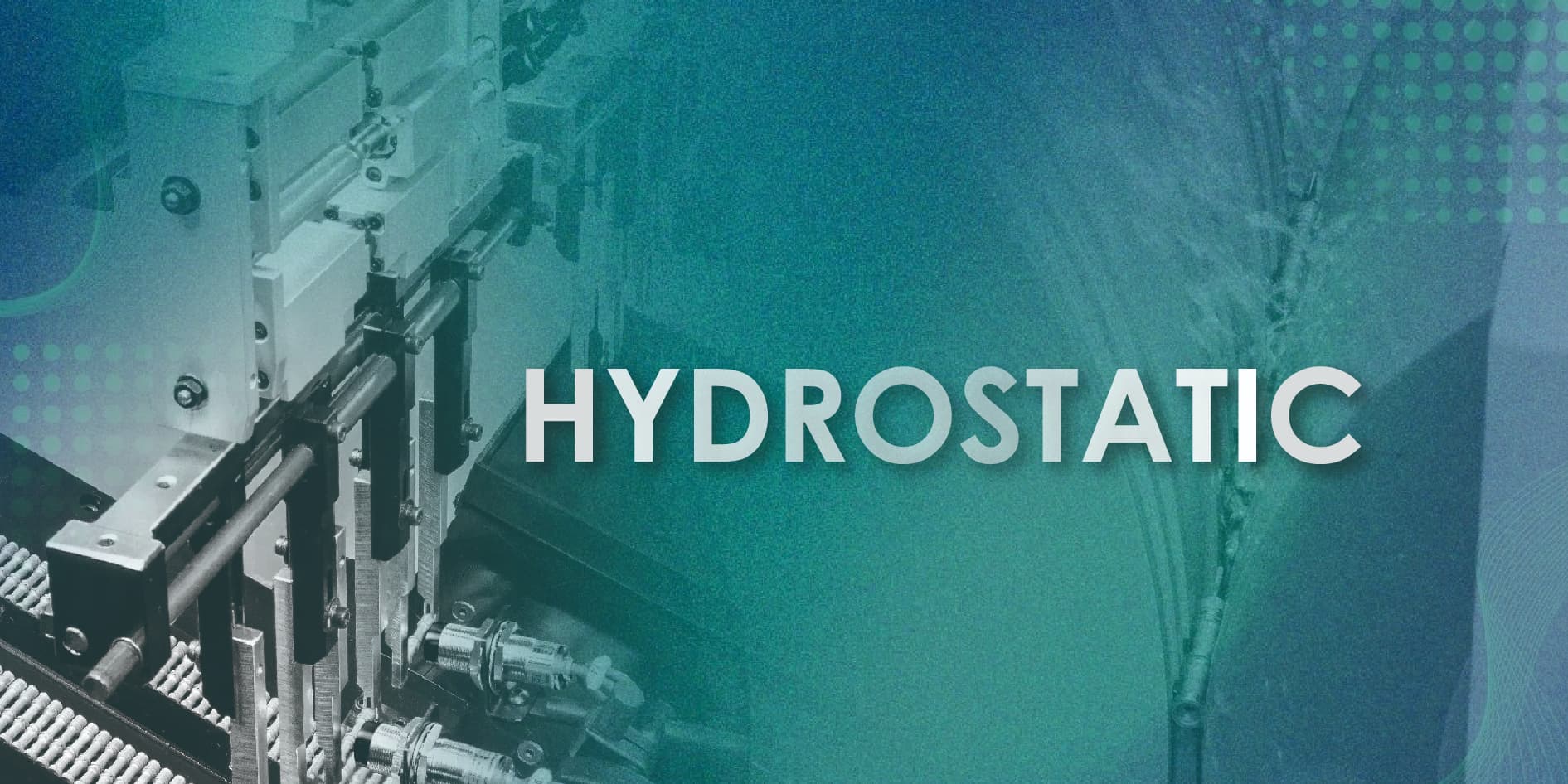
Hydrostatic Technology: The Key to Stable Centerless Grinding
In high-volume machining environments, equipment runs nonstop—grinding, dressing, and repeating cycles at high speeds. On the surface, everything seems smooth and stable. But in reality, what often impacts yield and efficiency the most isn't major equipment failure—it's the small, hard-to-detect changes that build up over time. Slight dimensional drift, unstable grinding wheel surfaces, and slower infeed speeds due to rising oil temperatures are just a few examples. These issues aren't typically caused by operator error. More often, they're signs that the machine's structural rigidity or long-term stability has reached its limits. In this article, we'll take a closer look at the fundamentals of centerless grinding and explain how hydrostatic technology helps solve these long-term stability challenges. By reducing internal friction and wear, hydrostatic systems eliminate hidden variations that can become bottlenecks—boosting both precision and production performance.
Centerless Grinding—No Centers, No Fixtures
Centerless grinding is a type of outer diameter (OD) machining that differs from conventional cylindrical grinders. Unlike traditional setups, centerless grinding does not require the workpiece to be held between centers or clamped by fixtures. This makes it an ideal solution for components that are difficult to support or grip securely during processing. Instead of relying on a chuck or centers, centerless grinding uses a three-point support system—consisting of a grinding wheel(G.W.), a regulating wheel(R.W.), and a work rest blade. This allows the part to rotate freely and be ground with high stability, even without direct clamping. The result is a streamlined process with fewer handling steps, better suited for automation and continuous production. This method is especially effective for components such as:
- Long and slender shafts (e.g., drive shafts, guide shafts)
- Piston rods and rollers
- Gear shafts
- Cylinder sleeves
- Copper bushings and small bearing sleeves
- High-volume or batch-produced parts
Because it efficiently handles hard-to-fixture parts, centerless grinding has become a preferred choice in high-throughput manufacturing environments.
Why a Centerless Grinder Needs to Be Stable?
Centerless grinding is inherently designed for high-volume, stable production. However, in real-world operations, several recurring issues often compromise this stability:
- Dimensional variation caused by thermal deformation or poor machine stability can reduce part consistency and lower yield in batch production.
- Intermittent movement in the slide during infeed can lead to fine surface marks and cosmetic defects, ultimately impacting surface roughness and dimensional precision.
- Abnormal spindle noise during startup or operation may indicate bearing wear, requiring frequent fine adjustments to maintain accuracy.
These issues are rarely the result of operator error. Instead, they typically stem from spindle wear and slide friction—core problems that hydrostatic systems are specifically designed to address. By reducing mechanical contact and improving motion control, hydrostatic technology helps ensure long-term machining stability and repeatability.
Hydrostatic Technology: The Backbone of Stable Production
In centerless grinding operations, machine stability plays a critical role in maintaining dimensional accuracy and production efficiency. Traditional hydrodynamic spindles and sliding components are prone to wear and thermal deformation, which often leads to fluctuations in grinding quality and frequent maintenance—ultimately limiting the machine's ability to run consistently over long periods. The Topking hydrostatic centerless grinder addresses these challenges with advanced hydrostatic technology. By applying a high-pressure oil film to support both the spindle and the slideways, the system significantly reduces mechanical friction and wear. This design not only enhances structural rigidity and thermal stability, but also extends the machine's service life. As a result, Topking's hydrostatic series delivers high-precision performance and consistently high yield, even during extended, high-volume production runs. In the following sections, we'll take a closer look at how hydrostatic spindles and hydrostatic slides work, and how each contributes to stable, efficient, and precise centerless grinding. You'll see how Topking's hydrostatic technology gives your production line a real edge in grinding stability and output.
Hydrostatic Spindle: Unlocking Higher Grinding Performance
The spindle is the core component responsible for maintaining grinding accuracy and machine stability in a centerless grinding machine. It mainly consists of two parts: the grinding wheel spindle and the regulating wheel spindle. The G.W. spindle drives the high-speed rotation of the grinding wheel, directly performing the cutting process and influencing the dimensional precision and surface quality of the workpiece. Meanwhile, the R.W. spindle controls the rotation speed and feed rate of the workpiece, ensuring it passes steadily and uniformly through the grinding wheel—maintaining continuous and consistent machining. The coordinated operation of these two spindles is key to achieving high efficiency and precision in centerless grinding.
Traditional hydrodynamic spindles rely on the negative pressure generated by spindle rotation to form a lubricating oil film. However, during startup, the oil film is not fully established, leading to metal-to-metal contact that causes spindle wear and accuracy fluctuations. Additionally, hydrodynamic systems are sensitive to variations in oil temperature and load, resulting in unstable oil film thickness that negatively impacts machining dimensions and yield. The R.W. spindle faces similar lubrication and wear challenges, affecting the stability of workpiece rotation and overall grinding quality.
Improving the lubrication and support system of the spindle is crucial for ensuring long-term stability and high precision in centerless grinding machines. Hydrostatic spindle technology addresses the limitations of traditional hydrodynamic spindles by providing a stable and full oil film support. This significantly reduces friction and wear while enhancing thermal stability and rigidity, ensuring the spindle maintains high accuracy and durability under various operating conditions. Key advantages of hydrostatic spindles include:
- Immediate Stability at Startup:
A complete oil film supports the spindle from the moment it starts, preventing metal-to-metal contact and initial wear. - Superior Thermal Stability:
Integrated oil temperature control prevents thermal deformation that can cause dimensional drift. - High Machining Precision:
Low vibration and high damping improve surface finish quality. - Extended Lifespan and Low Maintenance:
Wear-free startup dramatically reduces maintenance frequency and downtime.
Thanks to hydrostatic spindle technology, centerless grinding machines not only gain enhanced spindle durability and thermal stability but also achieve improved machining accuracy and productivity. This technology effectively lowers equipment maintenance demands, ensuring consistent quality during long, continuous production runs—making it an essential core support in high-precision manufacturing.
Hydrostatic Slideways: The Foundation of Stable and Accurate Grinding
In centerless grinding machines, the slideways play a critical role in controlling the regulating wheel spindle's feed motion, directly impacting feed accuracy and smoothness. This is especially important during fine feeding or long continuous grinding processes, where slideway performance determines dimensional consistency and surface finish quality. Traditional hardened slideways offer rigidity and damping but rely on metal-to-metal contact. At low speeds, they often suffer from stick-slip (crawling) effects, causing intermittent feed motion and micro-scratches on the workpiece surface. Additionally, wear accumulates over time, compromising positioning accuracy and increasing maintenance costs. Hydrostatic slideways use a high-pressure oil film to completely separate the contact surfaces between the guide rails and the sliding block, delivering the following technical advantages:
- Light and Low-Resistance Sliding:
Minimal force is needed to initiate slide movement, ensuring smooth motion even under heavy loads. - No Stick-Slip at Low Speeds & Vibration-Free at High Speeds:
Stable operation across all speed ranges supports precise micro-feed movements. - High Rigidity and Damping:
Capable of withstanding heavy loads while absorbing vibrations to maintain grinding stability. - Wear-Free and Long Lifespan:
Oil film support eliminates metal wear, enhancing overall system durability and reducing maintenance. - Outstanding Accuracy Retention:
Achieves ±0.5 μm positioning precision and fine feeding capability, ideal for advanced precision machining requirements.
Hydrostatic slideway technology enables centerless grinding machines to maintain stable motion and precise positioning even under high-precision micro-feeding conditions. This greatly improves product consistency and surface quality, establishing itself as a fundamental cornerstone in precision manufacturing.
Achieving Long-Term Stability in Grinding with Hydrostatic Solutions
Traditional centerless grinders experience cumulative wear on spindles and slideways during prolonged operation, leading to dimensional errors, fluctuating machining quality, frequent maintenance, and unexpected downtime. Many operators rely on experience-based adjustments to feed rates and dressing cycles to compensate for these errors. However, as precision requirements tighten, manual adjustments can no longer guarantee consistent performance and efficiency over long production runs. To address these challenges, TOPKING's hydrostatic centerless grinders utilize liquid hydrostatic support for both spindles and slideways, significantly reducing friction and wear while maintaining high stability and precision in motion. This technology not only extends equipment lifespan but also dramatically lowers maintenance frequency—making it ideal for long-duration, high-precision, and high-volume continuous machining.
With hydrostatic systems, TOPKING centerless grinders deliver stable dimensional control, minimizing variation and downtime risks caused by wear. This makes them the optimal upgrade for manufacturers seeking reliable processes and improved production efficiency.If you prioritize equipment stability and lower maintenance costs, TOPKING 's hydrostatic centerless grinders are the solution to consider first—helping you build a highly efficient and dependable machining line.
Reference Product of Topking's Hydrostatic Centerless Grinder:
NC series: H-4520-NC, H-5020-NC, H-5025-NC
CNC series: H-4520-CNC, H-5020-CNC, H-5025-CNC
Article Classification
Recent Articles
- How to Choose the Right CNC Grinder: Match the Control System and Machine to Your Production Needs
- Hydrostatic Technology: The Key to Stable Centerless Grinding
- Automated Match Grinding Solutions for Hydraulic Valve Components
- Struggling with Inefficient Grinding Operations?
- GRINDING MACHINE: essential for precision machining in manufacturing industry