- Home
- BLOG
- GRINDING MACHINE
- How to Choose the Right CNC Grinder: Match the Control System and Machine to Your Production Needs
How to Choose the Right CNC Grinder: Match the Control System and Machine to Your Production Needs
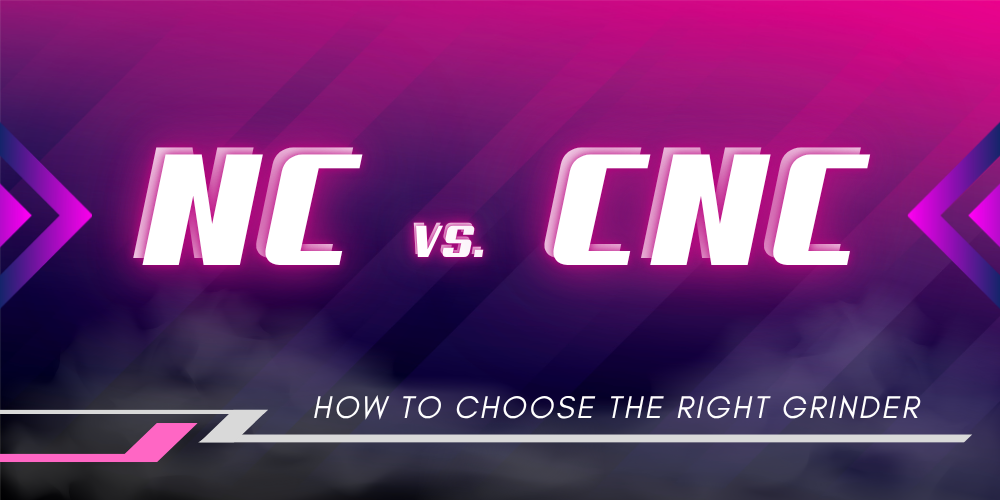
Many customers begin considering upgrading from manual grinders to CNC grinders only when their current operations “can no longer keep up.” This tipping point often comes when machining dimensions consistently hover near tolerance limits, production line efficiency slows down, workpiece precision requirements increase, yet aging machines break down frequently and maintenance struggles to keep pace with equipment issues. Alternatively, when orders increase and delivery pressures mount, existing equipment can only rely on operators' efforts to push through—resulting in worn-out staff and machines but stagnant productivity.
Though these problems might seem manageable through experience and fine-tuning, they are clear signals that the current equipment can no longer meet machining demands.Choosing the right CNC grinder at this stage is not just an equipment upgrade—it's a critical step to restore your production line's stability, efficiency, and controllability.Whether you are new to the grinding industry preparing to purchase your first machine, or a seasoned professional contemplating an upgrade from traditional manual grinders to NC or CNC grinders, the selection process can be daunting given the wide range of models and specifications available. This article will guide you through the advantages of CNC grinders and provide essential information to help you make an informed choice.
〈Further Reading: GRINDING MACHINE: essential for precision machining in manufacturing industry〉
CNC vs. NC Grinding Machines: A Complete Guide to Grinding Control Systems
When selecting grinding machines or upgrading production lines, a common question arises: “Should I choose an NC grinder or a CNC grinder? How do I select the right automated grinding machine control system?” While both fall under automated equipment, their underlying logic and applicable scenarios differ significantly.
What Is an NC Grinding Machine?
NC (Numerical Control)is an early digital control system that operates through control panels or programmable controller hardware modules to execute predefined machining processes. This type of system does not require complex programming input; instead, it relies on built-in commands such as fixed feed rates, movements, and dressing actions to complete basic machining cycles.
The operation of NC systems is intuitive and easy to learn, emphasizing simplicity and stability. It is particularly well-suited for production tasks with fixed machining requirements and high repetition. However, it has limitations in flexibility for adjustments, diverse machining paths, and multi-axis simultaneous control. Therefore, for production lines with uniform product types and stable large-volume output, NC offers a sufficient and cost-effective solution.
CNC Grinding Machines: Not Just an Upgrade, But a Strategic Transformation
CNC (Computer Numerical Control) uses computer-based machining that can read G-code programs and often provides a graphical user interface to configure various machining parameters. It goes beyond simple operation—offering a customized machining logic tailored to your specific workpiece requirements. You can flexibly adjust settings according to part demands, supported by multi-axis control, data output, automatic compensation, and other advanced features, significantly improving overall efficiency and precision.
If you are considering future automation integration—such as connecting robotic arms, sensors, or remote monitoring systems—CNC will be an indispensable core technology.
NC vs. CNC Grinding Machines: How to Choose the Right One for Your Needs
Understanding Manual, NC, 2NC, and CNC Grinding Machines: Essential Basics Before Choosing
When purchasing a grinding machine, brand and price are often top of mind—but one crucial factor is frequently overlooked: the control system. From traditional manual grinders to advanced CNC machines with multi-axis control and full automatic compensation, each type differs significantly in terms of structure, machining efficiency, and operational flexibility.
If you're at a turning point—replacing aging equipment or upgrading your production line—it's worth first understanding the basic characteristics of these four control types. By identifying the right level of automation, you'll be better equipped to choose a solution that truly fits your production needs.
.jpg)
.jpg)
.jpg)
.jpg)
Manual Grinding Machines: Where Experience Meets Skill
All operations are manually controlled—there's no automation in feed movement or wheel positioning. This type is ideal for single-piece, small-batch, and highly varied workpieces. The machining process relies heavily on the skill and experience of the operator.
-
Advantages:High flexibility, low cost, easy maintenance.
-
Limitations:Relies on manual labor for efficiency and consistency; unsuitable for high-volume production or frequent changeovers.
NC & 2NC Grinding Machines (Numerical Control): Entry-Level Automation
NC (Numerical Control)grinders use built-in commands—such as fixed feeds or wheel dressing—executed via a control panel to automate basic grinding cycles.
A 2-axis NC cylindrical grinder builds on this foundation by adding dual-axis control (typically X and Z axes), enabling more complex machining such as multi-step OD grinding. This significantly increases the level of automation compared to single-axis NC models.
-
Ideal for :small to mid-sized manufacturers aiming to reduce human error without fully transitioning to CNC.
-
Advantages :Intuitive operation, low learning curve, more cost-effective than CNC.
-
Key Difference :Single-axis NC focuses on basic infeed control, while dual-axis NC offers greater flexibility and a wider adjustment range.
CNC Grinding Machines: The Top Choice for High Precision and Automation
with a full computer-controlled system that enables multi-axis interpolation, automatic wheel dressing, size compensation, and even integration with loading/unloading automation. They are ideal for high-precision, high-volume, and frequently changing production tasks.
- Ideal for:smart manufacturing lines, automated machining, and workpieces requiring stable, repeatable production.
- Strengths:Excellent machining stability, high efficiency, and long-term reduction in labor dependency.
- Considerations:Higher initial investment and requires proper training and system planning.
Structural Differences Between Manual, NC, and CNC Grinding Machines
Choosing the right grinding machine involves more than just the level of automation—it also depends on the operation method, control structure, and machining flexibility.
To help guide your selection process, we've summarized the key structural differences between TOPKING's cylindrical grinders and centerless grinders. Use this comparison as a reference for your initial evaluation when selecting the most suitable grinding solution.
External Cylindrical Grinder Comparison Table
Model | Structural Features | Control Method | Recommended TOPKING Products |
---|---|---|---|
Manual External Cylindrical Grinder | Z-axis worktable driven by hydraulic system for lateral movement. X-axis grinding wheel head manually controlled by handwheel for infeed and retraction. | No servo motors or control modules. | — |
NC External Cylindrical Grinder | Z-axis worktable driven by hydraulic system for lateral movement. X-axis grinding wheel head driven by servo motor. | NC system with guided user interface, single-axis control allowing feed amount and speed setting. | — |
2NC External Cylindrical Grinder | Both X and Z axes driven by servo motors with ball screw mechanisms. | TOPKING's graphical control interface, dual-axis numerical control with basic safety protections. | T Series |
CNC External Cylindrical Grinder | Multi-axis servo drives supporting G-code control and multi-segment programming. | CNC systems (FANUC, Mitsubishi, Siemens) supporting G-code programming and GUI operation. | OGC Series X Series X-CAM Series |
Centerless Grinder Comparison Table
Item | NC Centerless Grinder | CNC Centerless Grinder |
---|---|---|
AXIAL COMBINATION |
One axis: X-axis:R.W. lower slide auto. in-feed control Two axes: Z-axis: Z-axis:G.W. auto. dressing (Vertical) X-axis:R.W. lower slide auto. in-feed |
|
〈Featured Products:Cylindrical Grinder 2NC | T series〉
〈Featured Products:Cylindrical Grinder CNC series | OGC series〉
〈Featured Products:Cylindrical Grinder CNC series | X series〉
〈Featured Products:Cylindrical Grinder CNC series | X-CAM series〉
〈Featured Products:Centerless Grinder Hydrostatic NC series〉
〈Featured Products:Centerless Grinder Hydrostatic CNC series〉
Is It Time to Upgrade? Key Signs You Need a CNC Grinding Machine
If you've started noticing these issues appearing regularly on your production floor, they're no longer isolated incidents—they signal that it's time to shift toward a more efficient and stable machining approach.
When existing equipment can’t keep pace with production demands, it often leads to lower yield rates, increased operator workload, and delays in delivery schedules. Upgrading to a CNC grinding machine not only addresses these pain points early but also optimizes the production process at its core: improving machining accuracy, reducing setup time, and minimizing dependence on skilled labor.
Most importantly, it lays a solid foundation for future automation and capacity expansion. This isn’t just about replacing equipment—it’s a strategic move to boost your competitiveness and enhance the resilience of your production line.
Signs It's Time to Upgrade to a CNC Grinding Machine – Overview Table
Sign | Description |
---|---|
Increased Production Load | Existing machines can no longer keep up with increasing production demands. |
Frequent Dimensional Errors | Dimensional instability requires multiple regrinding passes, reducing overall productivity. |
High Operator Turnover & Skill Retention Issues | Inexperienced operators are difficult to train, compromising production consistency and reliability. |
Complex Workpiece Geometry, Limited Machine Adjustability | Complex profiles or stepped parts increase setup difficulty and machining risk. |
Increased Automation Demand, Poor Equipment Integration | Older machines lack compatibility with robotic arms or automated loading/unloading systems. |
Rising Maintenance and Repair Costs | Spare parts are hard to source, leading to higher repair costs and increased downtime risk. |
Stagnant Production Efficiency | Machine design and control systems limit potential throughput and capacity improvements. |
Tightened Safety Regulations | New safety standards require guarding systems that are difficult to retrofit on older machines. |
Lack of Quality Monitoring and Data Management | Lack of real-time monitoring and data tracking makes it hard to ensure consistent quality. |
Growing Demand for Small-Batch, High-Mix Production | Long setup times reduce production flexibility for small-batch or high-mix jobs. |
Pressure to Reduce Energy Use and Carbon Emissions | New machines offer better energy efficiency and help reduce power consumption and carbon emissions. |
Limited Technological Upgrade Potential | Legacy machines are incompatible with remote monitoring, IoT, and smart manufacturing systems. |
The Automation Advantages of CNC Grinding Machines: 5 Key Benefits of CNC Integration
In today's pursuit of both productivity and quality, the automation potential of CNC grinders is gradually transforming traditional machining processes. Through advanced control technologies and peripheral integration, CNC grinders have evolved beyond standalone machines to become key components that synchronize seamlessly with entire production lines.
Below, we summarize the five major automation advantages and common configuration setups to help you design a more efficient manufacturing layout:
〈Further Reading:Automated Match Grinding Solutions for Hydraulic Valve Components〉
〈Further Reading:Hydrostatic Technology: The Key to Stable Centerless Grinding〉
1. Simplified Operation and Automated Workflow
The CNC control system can store multiple machining programs and process parameters in advance. Operators simply select the corresponding setup to quickly switch between products, significantly reducing changeover and setup times while minimizing dependence on skilled personnel.
2. Faster, More Accurate, and More Consistent Repeat Production
Automated machining processes effectively reduce human error, ensuring consistent dimensional accuracy and high-quality finishes across every batch. This precision automation is ideal for production lines seeking lean management, minimized labor intervention, and high-efficiency output.
3. Automatic Dressing & Compensation for Enhanced Machine Stability
Automatic wheel dressing and wear compensation functions allow for real-time dimensional adjustments and precision control during the grinding process. By eliminating the need for manual intervention, these features ensure consistent machining accuracy and stable product quality throughout long production runs, significantly enhancing operational efficiency.
4. Multi-Machine Integration for Synchronized Production Flow
CNC grinders can be integrated with loading/unloading robotic arms, measurement systems, and upstream/downstream equipment to form interconnected machining cells. This integration streamlines processes and synchronizes workflow, creating a truly high-efficiency automated production line.
5. Labor Savings and Increased Production Flexibility
By integrating automated loading/unloading and remote monitoring systems, CNC grinders enable lean or even unmanned production. This is especially suitable for night shifts and flexible production lines with small batches and high variety. It not only boosts night-shift productivity and reduces labor dependency but also enhances overall machine utilization and manufacturing efficiency.
Common CNC Grinding Machine Automation Solutions
Categories | Automation Features / Configuration Items | Description |
---|---|---|
Machine | CNC Control System | Programmed control enables fully automated grinding operations. |
Automatic Grinding Wheel Dressing | Automatic grinding wheel dressing maintains precise machining accuracy. | |
Automatic Wear Compensation | Automatic parameter adjustments ensure consistent dimensional stability. | |
Automation Accessories |
Touch Probe Gauge | The end-face measurement system uses sensors to determine the workpiece positioning reference. Commonly found on cylindrical grinders, this feature supports both fixed-length grinding and infeed-controlled grinding modes, effectively enhancing workpiece positioning accuracy and overall machining stability. |
Outer Diameter Measurement System | By utilizing contact or non-contact probes—such as infrared sensor technology commonly used in centerless grinders—the workpiece outer diameter is precisely controlled. This effectively prevents dimensional deviations, improves product interchangeability and assembly quality, and ensures high-precision machining requirements are met. | |
Auto Grinding Wheel Balancer | Automatic wheel balancing reduces grinding wheel vibration, enhancing the quality of the machined surface. | |
Gap Control | Using ultrasonic sensing technology, abnormal contact between the grinding wheel and workpiece is monitored in real-time, allowing early warning alerts. This effectively prevents grinder collisions, protects both the wheel and workpiece, reduces machine damage risks, and minimizes production downtime. | |
Linear Scale for Z-axis | High-precision optical encoders measure machine axial displacement and position, combined with a closed-loop feedback control system to effectively ensure dimensional stability. This reduces cumulative errors and enhances machining accuracy and production efficiency. | |
Loading/ Unloading Devices |
Robotic Loading and Unloading | Automated workpiece loading and unloading systems enable unmanned material handling, improving production automation efficiency and machining continuity while reducing labor costs. |
Automatic Feeding and Storage Tray | Continuous feeding systems ensure uninterrupted production line operation, enhancing manufacturing efficiency and capacity while reducing downtime and material shortage risks. | |
Automatic Workpiece Collection | Automated sorting and stacking systems for finished parts reduce manual handling, increase production efficiency, and improve product management accuracy, enabling intelligent manufacturing processes. | |
Multi-Machine Networking | Integrated automation with upstream and downstream equipment creates a continuous production line system, enhancing manufacturing efficiency and product quality stability. |
Choosing the Right Grinding Machine Control System Based on Your Needs
Although both NC and CNC are automated grinding machine control systems, they differ significantly in system flexibility and production applications. NC systems feature a relatively simple structure and intuitive operation, making them suitable for stable, low-variation machining environments. They offer the advantages of a low learning curve and cost-effectiveness.
In contrast, CNC grinders provide high flexibility and intelligence, capable of handling diverse workpieces and complex machining requirements. Beyond supporting multi-axis control and program switching, CNC systems can integrate robotic arms, sensors, and automated measurement devices to create a fully connected smart manufacturing process. For production lines that prioritize automation, multi-product variety, and flexible manufacturing, CNC systems are undeniably the forward-looking choice.
Before selecting equipment, it's advisable to comprehensively assess your machining tasks, production mode, future expansion plans, and budget allocation. Choosing the right control system is not merely a technical decision; it directly impacts the overall production line’s return on investment and future growth potential. A well-informed choice will not only boost current efficiency but also establish a solid foundation for sustained development.
〈Further Reading:Struggling with Inefficient Grinding Operations?〉
Conclusion
Whether you are introducing automation equipment for the first time or upgrading an existing production line, understanding the core differences between NC and CNC grinders is the crucial first step in selecting the right machine.If you're still undecided, consider this self-assessment: Does your production prioritize stable mass manufacturing, or is greater flexibility and future scalability more important? What is your budget range? Once these criteria are clear, the optimal solution will naturally follow.
If you still have questions about selecting the right control system or want to learn more about our real-world application cases, feel free to download our product catalog or contact us directly. We are committed to providing expert, customized advice and technical support to help you find the best solution tailored to your needs.
Article Classification
Recent Articles
- How to Choose the Right CNC Grinder: Match the Control System and Machine to Your Production Needs
- Hydrostatic Technology: The Key to Stable Centerless Grinding
- Automated Match Grinding Solutions for Hydraulic Valve Components
- Struggling with Inefficient Grinding Operations?
- GRINDING MACHINE: essential for precision machining in manufacturing industry