- Home
- BLOG
- GRINDING MACHINE
- GRINDING MACHINE: essential for precision machining in manufacturing industry
GRINDING MACHINE: essential for precision machining in manufacturing industry
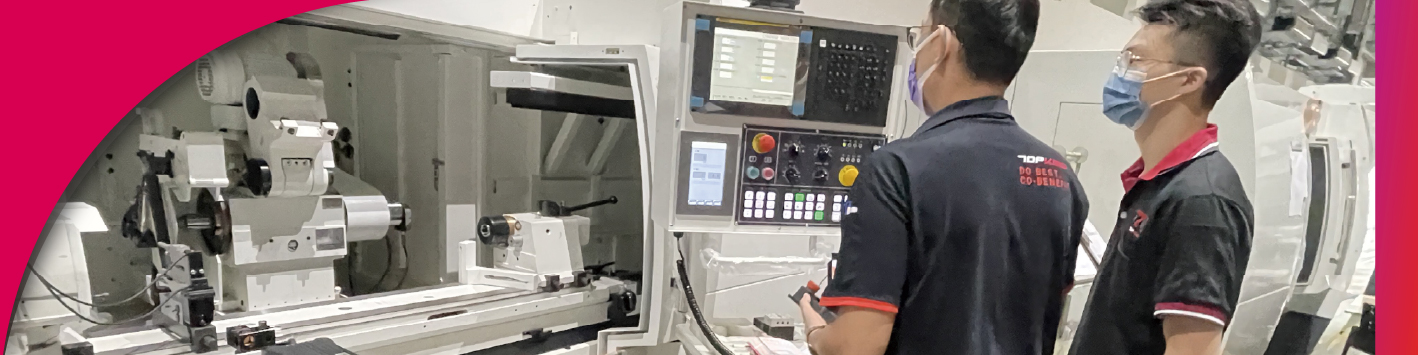
For those of you who may be unfamiliar with the manufacturing sector! Have you ever wondered which tools to use when faced with the need for precision machining of mechanical parts? This article will introduce you to a highly regarded tool in the manufacturing industry – the grinding machine. Perhaps you've heard about it, but the specific usage and advantages might still be unclear. Let's delve into the world of grinding machines in the simplest and most understandable way, enriching your knowledge of the manufacturing industry!
WHAT IS A GRINDING MACHINE?
Much like using sandpaper to refine wood or stone, a grinding machine is a specialized tool widely employed in the manufacturing sector. Its primary task is to ensure that manufactured parts achieve superior surface quality and precision, akin to performing delicate cosmetic surgery on components. This indispensable role positions the grinding machine as a key player in manufacturing, providing crucial support for the overall quality of the final product.
IT'S EASY TO LEARN HOW IT WORKS
Grinding machining is renowned for its exceptional high precision, centered on the core action of grinding or, alternatively, abrasion. Through meticulous removal of excess material from the workpiece using a precision grinding tool, it achieves the desired shape, dimensions, and a flawlessly smooth surface. This refined grinding process utilizes a high-speed rotating abrasive tool, typically a grinding wheel, for precise cutting, elevating both precision and surface quality of the workpiece. Widely embraced in the global manufacturing industry, grinding machining stands as the preferred choice for producing top-tier, high-precision components.
COMMON TYPES OF GRINDING MACHINES
In the manufacturing industry, grinding machines play an indispensable role. Here's a brief introduction to six common types of grinding machines, each offering unique solutions for different workpiece requirements, injecting diversity and efficiency into the manufacturing process.
1. CYLINDRICAL GRINDING MACHINE
This type of grinder is designed to focus on grinding the outer diameter and end faces of workpieces, making it particularly suitable for processing various shapes, including cylinders, cones, ellipses, cams, and crankshafts. Its uniqueness lies in the requirement for the workpiece to have a central rotating axis, ensuring grinding precision and showcasing exceptional versatility in processing various shapes.
2. CENTERLESS GRINDING MACHINE
Boasting high productivity and the ability for continuous and batch production, this type of grinder is widely employed in the grinding processing of axial components that require large-scale production, such as those in the automotive, electrical appliances, and precision mold industries. The grinding process eliminates the need for centering the workpiece's axis, relying on the grinding wheel, in conjunction with an regulating wheel, to control the workpiece's rotation and generate the feed rate. The workrest (blade) sustains the workpiece throughout the grinding process, ensuring the final workpiece achieves high precision in dimensions, roundness, cylindricality, and surface smoothness.
3. INTERNAL GRINDING MACHINE
Specifically designed for machining workpiece inner holes, the internal grinding machine utilizes small grinding wheels as tools to precisely remove excess material from the inner hole surfaces, meeting the high-precision requirements of manufacturing and assembly. This type of grinder finds extensive applications in processing the inner hole surfaces of axial and sleeve-type workpieces, including tapered holes, through-holes, and blind holes.
4. VERTICAL GRINDING MACHINE
With its distinctive structural features, this type of grinder is immune to the vibrations and deviations caused by the weight of the workpiece fixture. It is particularly suitable for manufacturing large, heavy, and irregularly shaped workpieces. The grinding wheel's spindle is parallel to the worktable, allowing for vertical grinding, making it adept at precise grinding processes for internal holes and end faces.
5. SURFACE GRINDING MACHINE
This type of grinder is primarily utilized for grinding the flat or contoured surfaces of workpieces, processing them through reciprocating motion. The main tool employed is the outer circular edge of a grinding wheel, commonly applied in the manufacturing of components that require smooth surfaces, such as molds, gears, and guideways. The unique processing method of surface grinding machines allows for flexible handling of various surface shapes, including flat, concave, and convex surfaces.
6. TOOL GRINDER
This is a grinder specially designed for the grinding, sharpening, and processing of various tools, blades, and drills. It is used for the precision adjustment of cutting edges, simultaneously shaping and ensuring the sharpness of the tool's cutting edge to enhance accuracy and lifespan. Serving as an indispensable tool in the manufacturing industry, it delivers efficient cutting performance.
WHEN WOULD PEOPLE COMMONLY USE GRINDERS IN EVERYDAY LIFE?
1. AEROSPACE INDUSTRY
In the aerospace industry, grinding machines are frequently utilized in the manufacturing of aircraft engine components and lightweight structural parts to ensure stability during flight, ensuring the overall safety of the aircraft.
2. AUTOMOTIVE INDUSTRY
In the automotive industry, precision components for engine parts and the transmission system, such as crankshafts and camshafts, are of paramount importance. The high precision is crucial for the seamless coordination between parts during engine operation. Grinding machine processes ensure that these components achieve optimal dimensions and surface smoothness, contributing to excellent and reliable automotive performance.
3. MECHANICAL COMPONENTS
In the manufacturing of medical devices, precision is a critical indicator, especially for artificial joints or implantable instruments. The surface smoothness directly influences their compatibility with human tissues, reducing the risks of friction and tissue damage to ensure the success of surgeries and the safety of patients. These instruments require a perfect fit with human tissues to guarantee the success of surgeries and the safety of patients. Grinding machines can achieve extremely high processing precision, meeting the medical industry's stringent standards for accuracy.
4. HARDWARE, MECHANICAL & 3C INDUSTRY COMPONENTS
In our daily lives, many hardware components, communication devices, and mechanical parts come in various complex shapes, with different hardness levels, and require the processing of different types of metals and non-metal materials. These workpieces may undergo grinding machine processes. Grinding machines not only address the challenges of machining intricate shapes but also enhance precision and quality. The application of grinding machines significantly improves the overall quality of products. Through precise grinding of materials, grinding machines can produce smooth, flat surfaces, reducing friction and wear between parts, thereby extending the lifespan of products.
MASTERING THE GRINDER INITIATES A REVOLUTION IN HIGH EFFICIENCY
The Taiwanese manufacturing industry is globally renowned for its excellent craftsmanship, and the grinder, as a crucial element in industrial production, not only represents the continuous evolution of technology but is also a manifestation of intelligence and precision. In the pursuit of high efficiency and unwillingness to compromise on accuracy in industrial production, the grinder has become an indispensable and efficient assistant. It not only performs grinding tasks efficiently but also maintains minimal surface roughness. Based on different processing methods, grinders can be further categorized into cylindrical grinders, centerless grinders, internal grinders, vertical grinders, tool grinders, surface grinders, etc., to meet various processing needs and address diverse machining challenges.
TOPKING's grinders are highly praised globally for their outstanding product performance and reliable quality. Today, TOPKING is not just a grinder manufacturer but also a solution provider in the field of grinding. We are committed to sharing practical experiences with various grinders, helping you discover the potential in the field of grinding. Simultaneously, in terms of improving economic efficiency, TOPKING will provide practical solutions to assist you in building a more cost-effective production process, working together to usher in a new era of efficient production.
Article Classification
Recent Articles
- How to Choose the Right CNC Grinder: Match the Control System and Machine to Your Production Needs
- Hydrostatic Technology: The Key to Stable Centerless Grinding
- Automated Match Grinding Solutions for Hydraulic Valve Components
- Struggling with Inefficient Grinding Operations?
- GRINDING MACHINE: essential for precision machining in manufacturing industry