- Home
- Products
- Centerless Grinder
- Hydrostatic CNC series
- H-4520-CNC
Hydrostatic CNC series
H-4520-CNC
CENTERLESS GRINDERINTRODUCTION
The H Series is built around static pressure technology, offering high precision, low wear, and long-term stability to ensure consistent processing quality. The wheel spindle, regulating wheel spindle, and feeding axis (lower slide rail) are supported by a static pressure oil film, allowing for contact-free operation. This prevents mechanical wear and maintains high precision even during extended use.
Its high rigidity and damping characteristics effectively reduce vibration, enhancing stability and surface quality during machining. The minimum feed rate is as low as 0.0005mm, ensuring excellent roundness, surface quality, and dimensional accuracy of the workpiece.
| CAPACITY
Standard Grinding Range (dia.): Ø1 ~ Ø45 mm
Grinding Wheel (O.D. x width x I.D.): Ø455 x 205 x Ø228.6(7A) mm
Linear Velocity: 33 m/sec(45 m/sec)
Regulating Wheel (O.D. x width x I.D.): Ø255 x 205 x Ø127(7A) mm
R.W. Speed: 10 ~ 300 rpm
Max. Infeed Length: 200 mm
MACHINE FEATURE
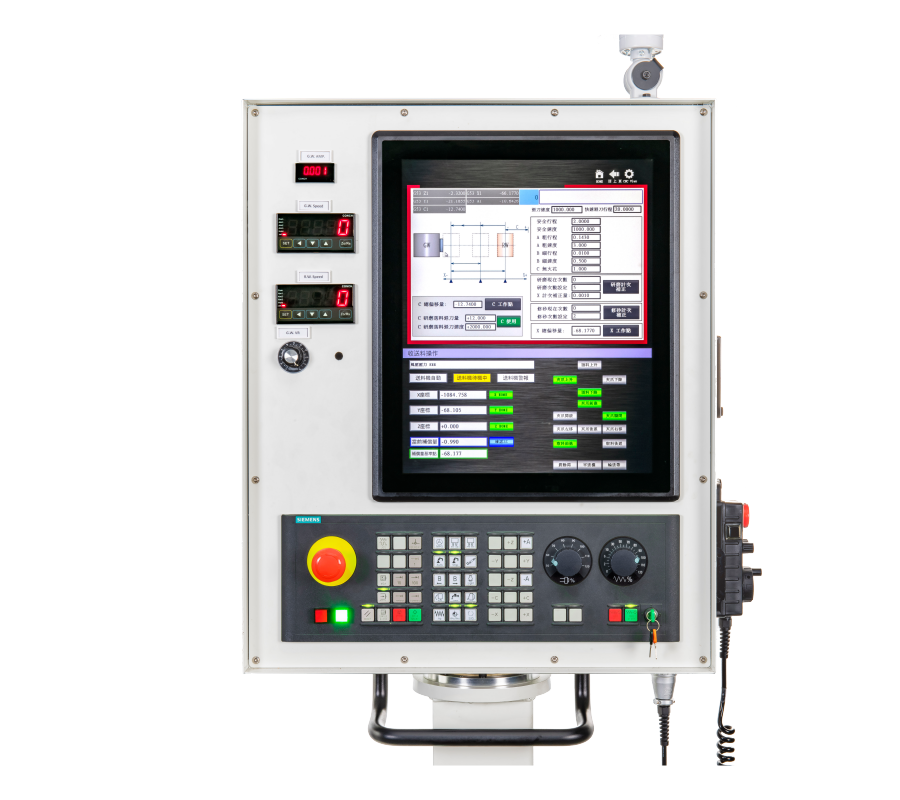
USER-FRIENDLY OPERATION SYSTEM
■ Latest CNC technology. Clever program edit for various kinds of component grinding applications.
■ Install several shortcuts for practical functions and an emergency stop button on the operation panel.
■ Improve working safety and efficiency.
■ Flexible software for cooperating with various auto. loading and unloading system (opt. individual design).
■ MITSUBISHI/FANUC/SIEMENS systems are available.
RIGID MACHINE BASE
■ The machine structure is made of high-quality Meehanite cast iron, which is processed after being heat treated and stress relieved before machining. The slide is hardened by high frequency and precision ground. The material of the machine structure is stable, has no doubt of deformation, and has excellent wear resistance.
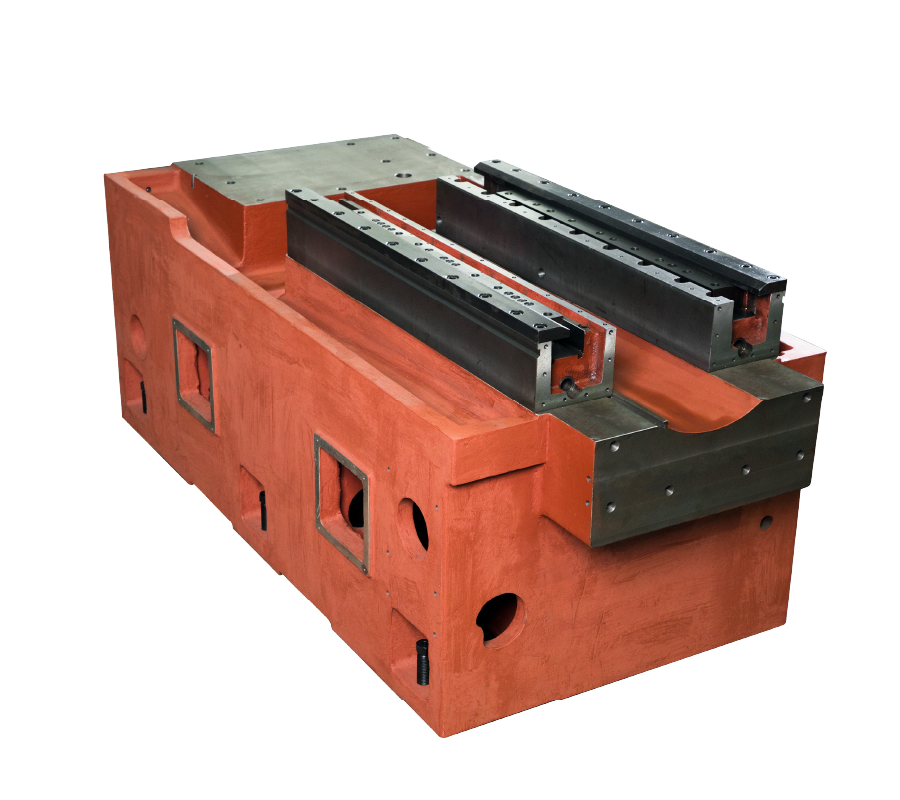
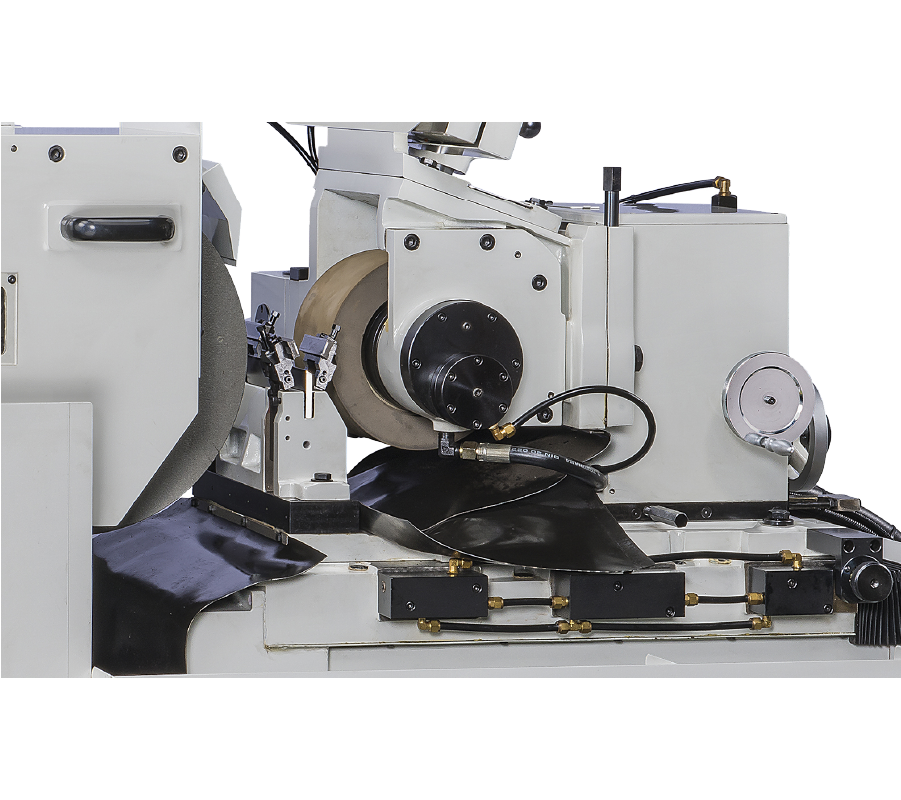
ADVANTAGE OF HYDROSTATIC SPINDLE AND SLIDE RAIL
■ No abrasion between metal to metal, improving the service life of the machine.■ Extremely low metal friction. Low-temperature rise during processing, not easy to deform, improves processing stability and component accuracy.
■ High-pressure oil film wraps around the spindle, suitable for high-speed rotation.
■ High-precision application and constant rotation ensure rotation accuracy.
OIL COOLANT SYSTEM
■ The oil coolant system is equipped with an oil cooler to effectively maintain a constant oil temperature and prevent the spindle from affecting the machining accuracy due to changes in oil temperature.
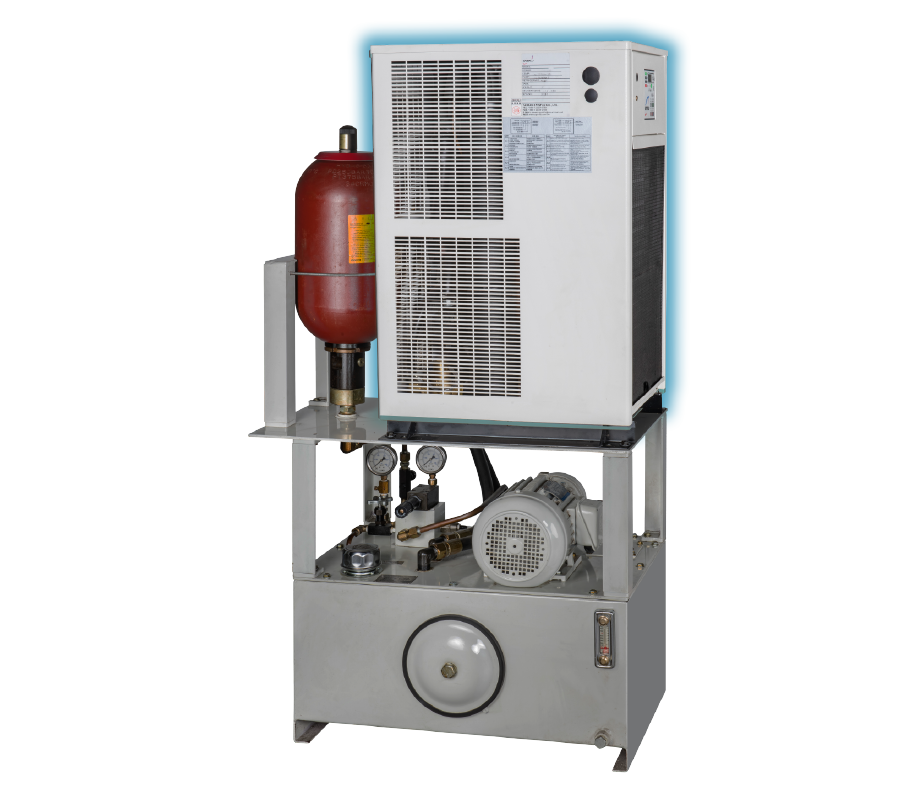
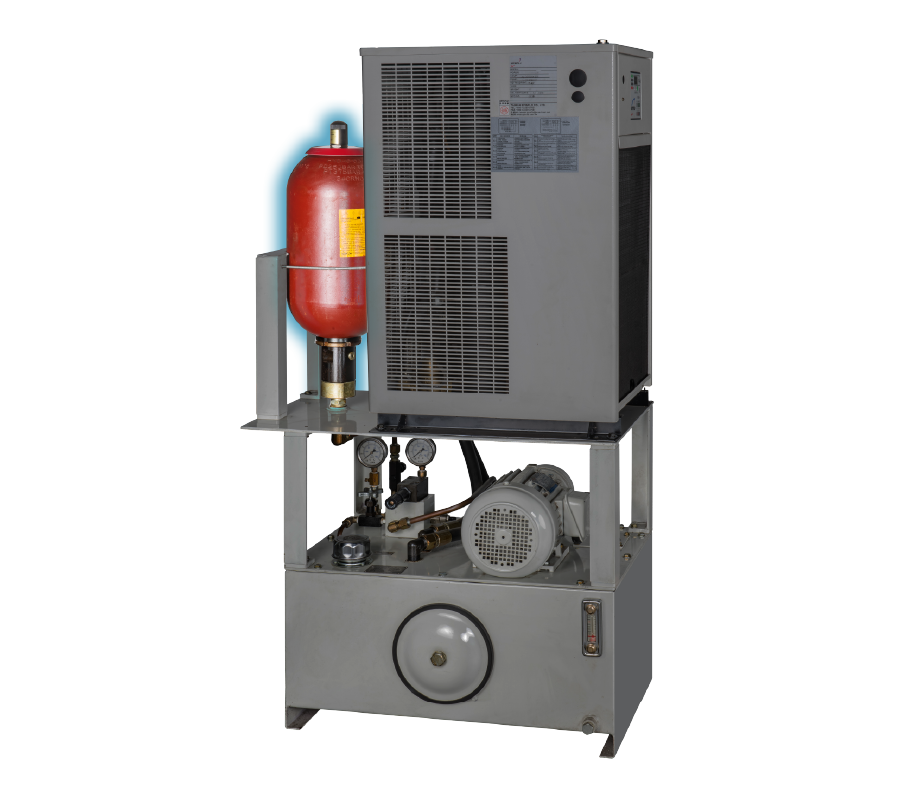
ACCUMULATOR FOR PROTECTION DEVICE
■ The special pressure accumulator design can make the hydrostatic oil return to the hydrostatic system of the main shaft when the pressure drops due to power failure. It can avoid the damage caused by the momentary loss of static pressure oil film caused by power failure when the spindle is running at high speed.
HYDROSTATIC GUIDEWAY CONSTRUCTION
■ R.W. lower slider (infeed axis) is a hydrostatic guideway construction design. This provides various features such as extremely smooth and fast sliding movement, high precision feeding accuracy, and stable grinding accuracy.
■ The lower feeding axis is driven by a servo motor cooperated with a harmonic reducer. The advantages are reducing backlash, increasing torque, improving grinding efficiency, and stabilizing precision grinding quality.
■ The minimum manual feeding amount of the micro-adjustment type device is 0.001 mm. In addition, the minimum feeding amount can be set by numerical control to 0.0001 mm which can meet the precision requirements of various components.
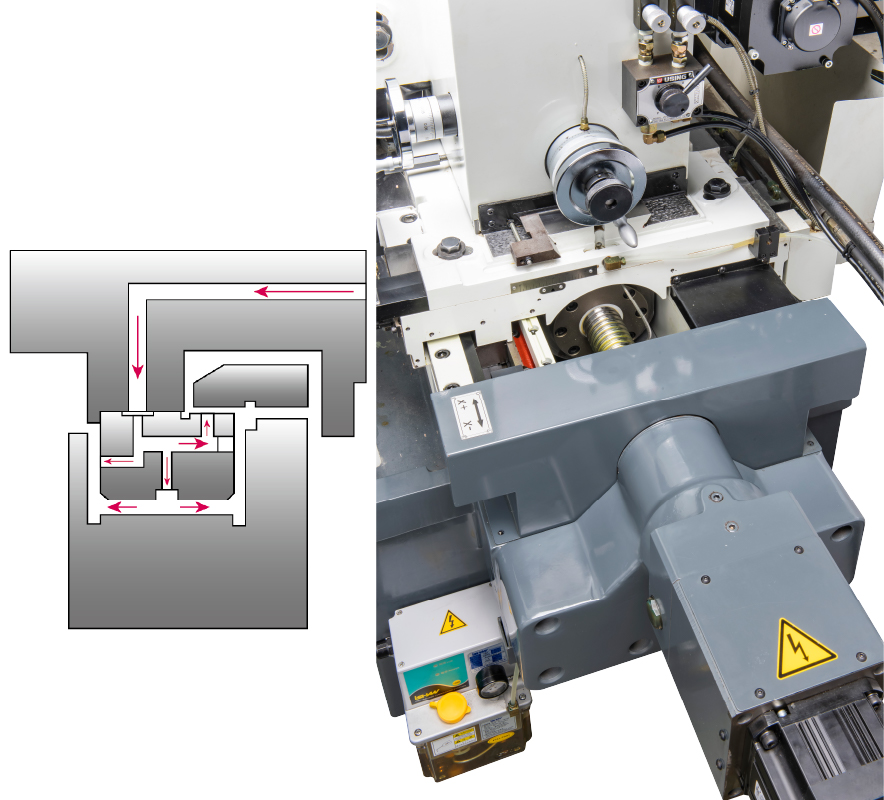
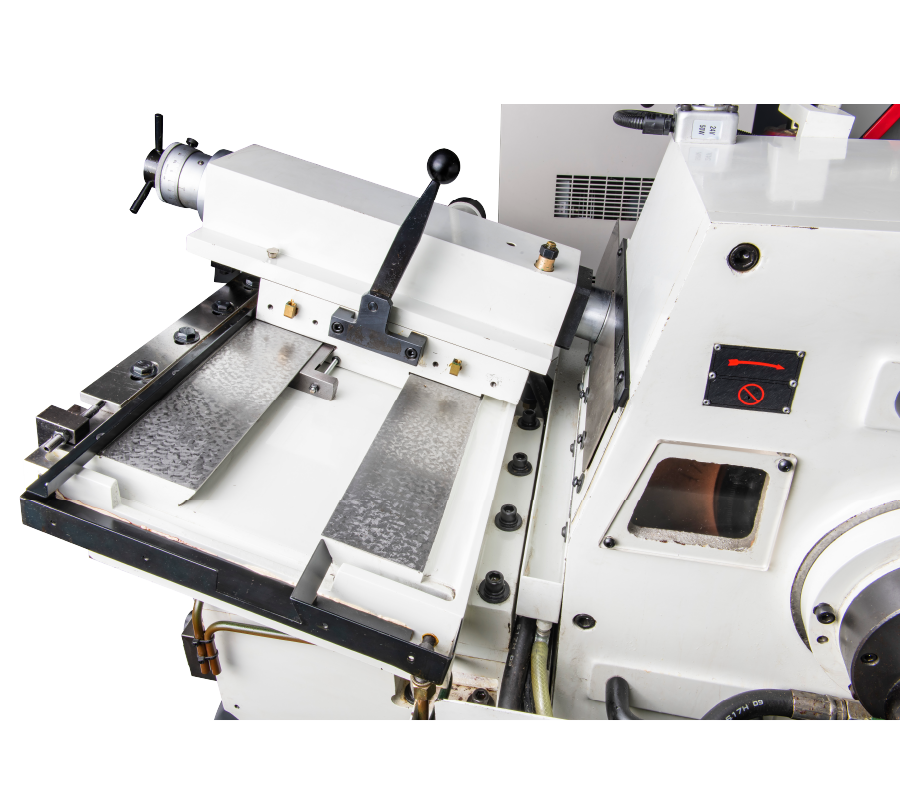
STABLE GRINDING WHEEL AUTO. DRESSING UNIT(FOR 1-AXIS ABOVE)
■ The lower slideways of the grinding wheel dressing seat are designed as a concave dovetail structure. This design combines with an extra-large sideway to greatly improve the stability of the grinding wheel device.
DRESSING DEVICE OF R.W. & G.W. (FOR 1 AXIS)
■ Dressing structure is made of special alloy cast iron and is heat treated for wear resistance.
■ The dressing device is driven front and rear by hydraulic pressure, and it can also be matched with a servo motor for profile dressing.
■ Variable dressing speed.
■ The Dressing device of R.W. can be adjusted according to the components' requirement to ensure the accuracy of the cylinder.
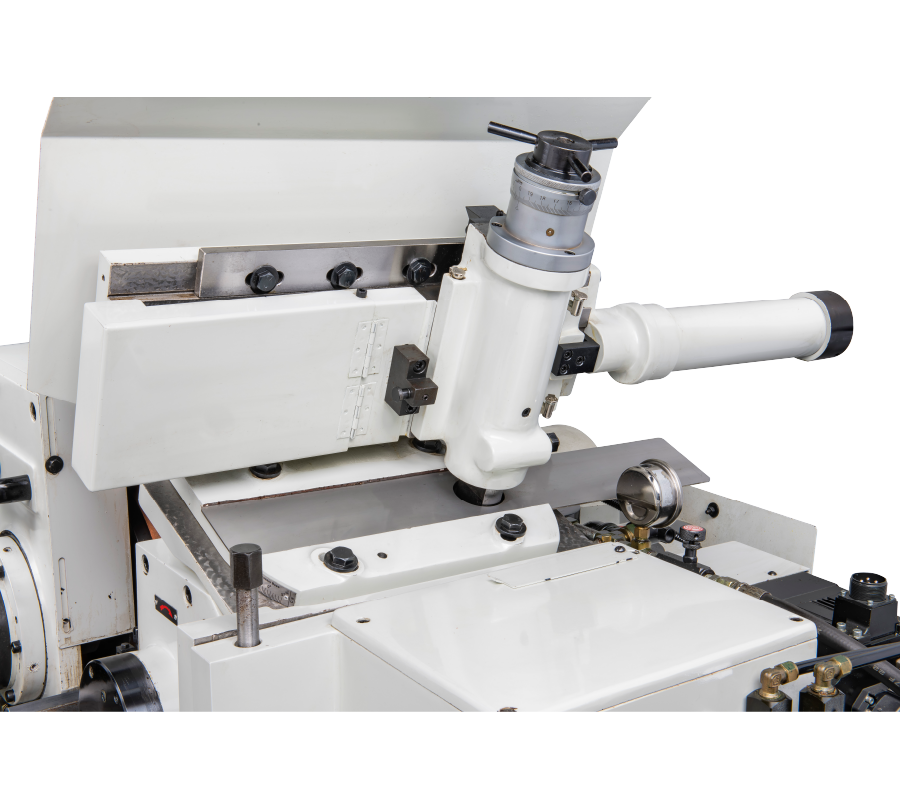
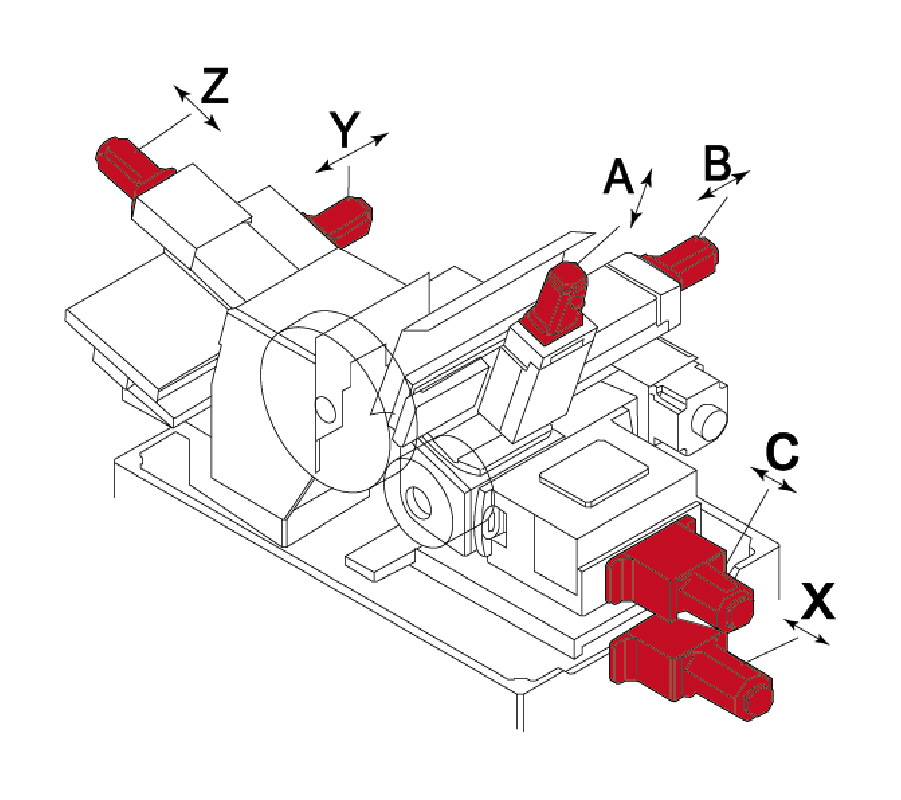
AXIAL COMBINATION FOR CNC SERIES
■ Z-axis: Grinding wheel auto. dressing (Vertical)
■ Y-axis: Grinding wheel auto. dressing (Horizontal)
■ A-axis: Regulating wheel auto. dressing (Vertical)
■ B-axis: Regulating wheel auto. dressing (Horizontal)
■ C-axis: Regulating wheel auto. upper slide auto. Infeed
■ X-axis: Regulating wheel auto. lower slide auto. Infeed
SPECIFICATION
Capacity | |
---|---|
Standard Grinding Range (dia.) | Ø1 ~ Ø45 mm |
Max. lnfeed Length | 200 mm |
Auto. Infeed Min. Increment | 0.0005 mm |
Grinding Wheel | |
Size (O.D. x width x I.D.) | Ø455 x 205 x Ø228.6(7A) mm |
Linear Velocity | 33 m/sec (45 m/sec) |
Regulating Wheel | |
Size (O.D. x width x I.D.) | Ø255 x 205 x Ø127(7A) mm |
Speed | 10 ~ 300 rpm |
Tilt Angle | +5° ~ -3° |
Swivel Angle | ±5° |
Hand wheel Graduation | |
Upper Slide Feed | 4 mm/rev. (0.05 mm/graduation) |
Lower Slide Micro-Feed | 0.08 mm/rev. (0.001 mm/graduation) |
Trimming Device | 2 mm/rev. (0.01 mm/graduation) |
Drive Motors | |
Grinding Wheel | 7.5 kW (6P) |
Regulating Wheel | 3.5 kW (servo motor) |
Lower Slide Feed Motor (X-axis)(NC one axis) | 1.0 kW |
Hydraulic Pump | 1.5 kW |
Coolant Pump | 0.18 kW |
Hydraulic Oil Chiller | 0.37 kW |
Tank Capacities | |
Hydraulic Oil Tank | 90 L |
Coolant Tank | 160 L |
Machine | |
Dimension (L x W x H) | 3050 x 1710 x 2100 mm |
Net Weight | 4300 kg |
* The mentioned specifications & dimensions are subject to change without notice.
ACCESSORIES
STANDARD ACCESSORIES
■ Grinding Wheel and Flange x 1 set
■ Regulating Wheel x 1 set
■ Infeed Work Rest and Carbide Blade x 1 set
■ Thrufeed Work Rest and Carbide Blade x 1 set
■ Diamond Tools (2 pcs/set) x 1 set
■ Electric System x 1 set
■ Hydraulic System (with oil coolant and accumulator) x 1 set
■ Coolant System x 1 set
■ Work Lamp x 1 set
■ Tools (Leveling Pad) and Tool Box x 1 set
■ Wheel Balancing Stand & Arbor
■ Profile Grinding Attachment
■ Grinding Wheel Ionization Dressing Device
■ Hydraulic Work Ejector (Infeed Grinding)
■ Manual Feeder For Infeed Grinding (Up and Down)
■ Auto. Loading Attachment (Thrufeed Grinding)
■ Automatic Feeder (Thrufeed Grinding)
■ Auto. Unloading Attachment (Thrufeed Grinding)
■ V Type Supporter for Long Bar Grinding
■ Auto. Loading and Unloading Attachment (Infeed Grinding)
■ Vibratory Feeder (Thrufeed Grinding)
■ Fully Splash Guard
■ Magnetic Coolant Separator
■ Paper Filter
■ Hydro cyclone Coolant Separator