CNC CAM grinding
X-3550CAM
CNC CAM grindingINTRODUCTION
TOPKING's X-CAM series is the specialized design for eccentric and not circular components grinding. It’s applied to eccentric, cam shaft, crank shaft, polygon punch grinding. It’s especially suitable for use in the automotive, automation equipment, mold industries. Control system equips with advanced SIEMENS controller and cooperates with TOPKING latest GUI work interface, increase parameter setting efficiency. Providing the best accuracy performance and operating environment.
| CAPACITY
Swivel Over Table: Ø370 mm
Distance Between Center: 500 mm
Max. Grinding Dia.: Ø350 mm
Max. Grinding Length: 500 mm
MACHINE FEATURE
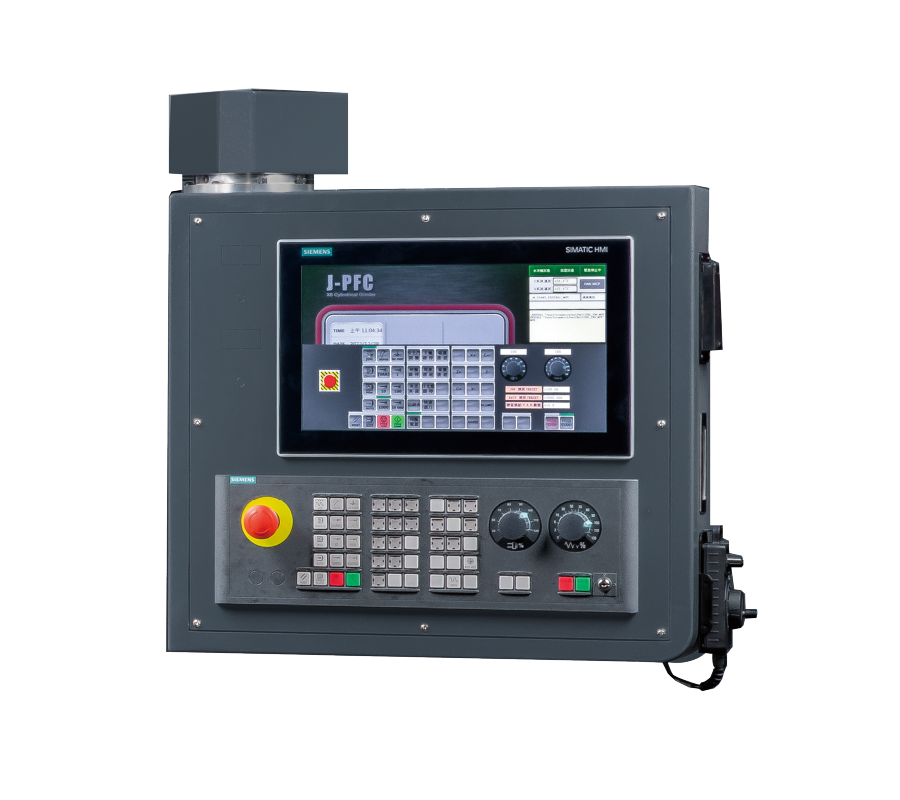
USER FRIENDLY OPERATION SYSTEM
■ Equipped with SIEMENS 840Dsl control system. Built-in TOPKING’s latest version graph conversational operate interface includes crankshaft and camshaft grinding application. Make work easier! Moreover, operating with CAD/CAM software (optional accessories) easy to preprogram custom-made grinding graphics. Provide a flexible and humanized operating environment.
RIGID MACHINE BASE
■ High rigidity machine base made of Meehanite cast iron through annealing and aging treatment.
■ Slideway through high-frequency hardening and precision grinding process. Machine base with stable material and strengthen construction for deformation-free and outstanding wear resistance.
■ The machine’s structure is different from the light weight design philosophy in the past; it substantially consolidates the rigidity of the body and parts structure, takes being more stable as the appeal, and adopts thick a and solid sliding seat mechanism, slide way 1 V 1 flat structure providing the best precision and stability of moving when doing grinding.
.png)
.jpg)
WORK TABLE
■ The work table is permanently bolted to the machine. The cross slide design is adopted to reduce the travel. It can improve working speed and precision stability.CROSS-SLIDER DESIGN & AXIS GUIDANCE
■ The X and Z axes feature a cross-slide configuration, the wheelhead traverses along the Z axis, leading to a reduction in the required workspace.
■ The X-axis is driven directly by a linear motor, in conjunction with the box-way system, providing substantial structural support. This design empowers the machine to withstand significant grinding forces and torque, ensuring a stable grinding process.
■ Incorporating a 1V1 flat guideway with generous guide spacings, establishes a robust foundation for the movement of the cross-slide assembly and the wheelhead seat.
■ The slideway surfaces feature a worn sheet, demonstrating exceptional durability and anti-abrasion properties, poised to meet the demands of prolonged grinding operations.
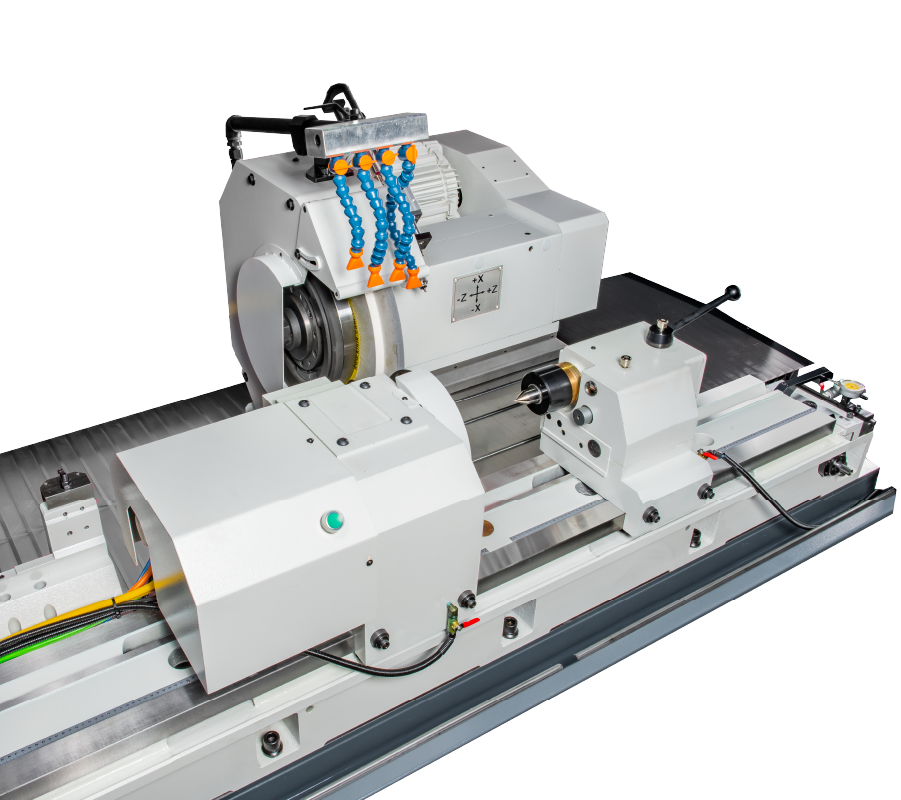
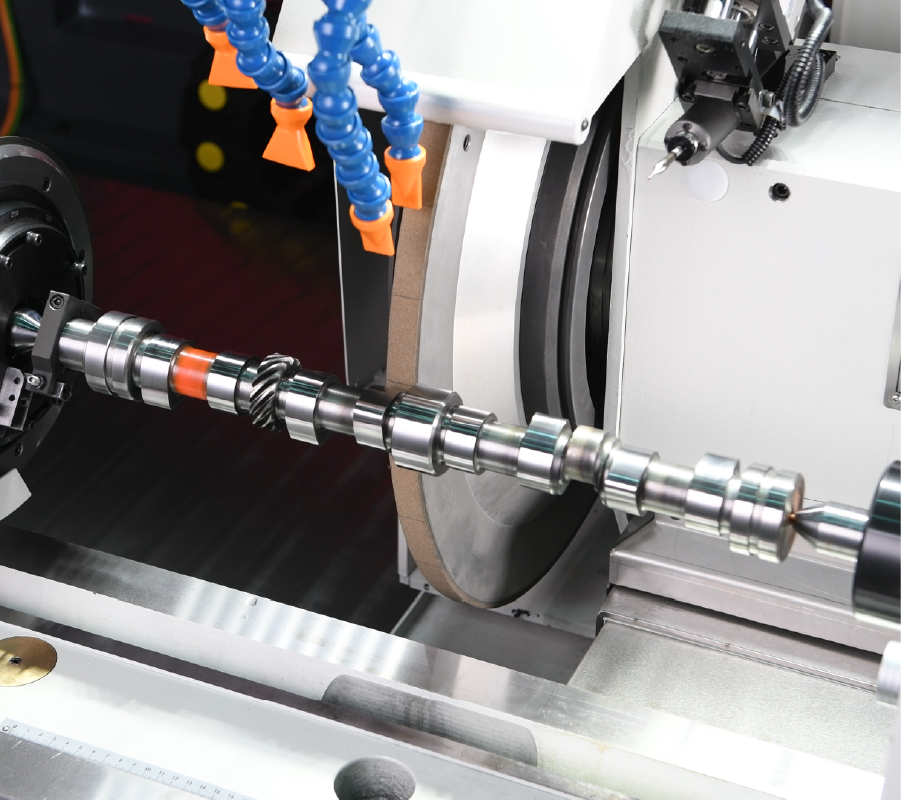
X-AXIS DRIVE BY LINEAR MOTOR
■ X axis is driven by a linear motor directly, with no backlash for achieving more precise position control.
■ Cross-slider construction with high-speed precision linear motor and closed-loop control linear scale on X axis. Apply the smoothest working condition with the C axis.
■ Moving speed could reach 15000 mm/Min.
■ Linear motors constitute of coil and permanent magnets. No attrition for longer uses use and contributes to energy savings and increased efficiency.
WHEELHEAD CONSTRUCTION
■ Bearing type of G.W. spindle adopts precision bearings, which have a long service life and are relatively easy to replace, repair, and maintain.
■ The G.W. spindle is made of high-quality alloy steel SNCM-220, which has undergone multiple treatments such as normalization, quenching and tempering, carburizing heat treatment, and cryogenic treatment. Afterwards, precision grinding and mirror treatment are carried out, and the surface hardness reaches above HRC62°. Guarantee no deformation, wear resistance, high precision forever.
%400_5x-x-cam.png)
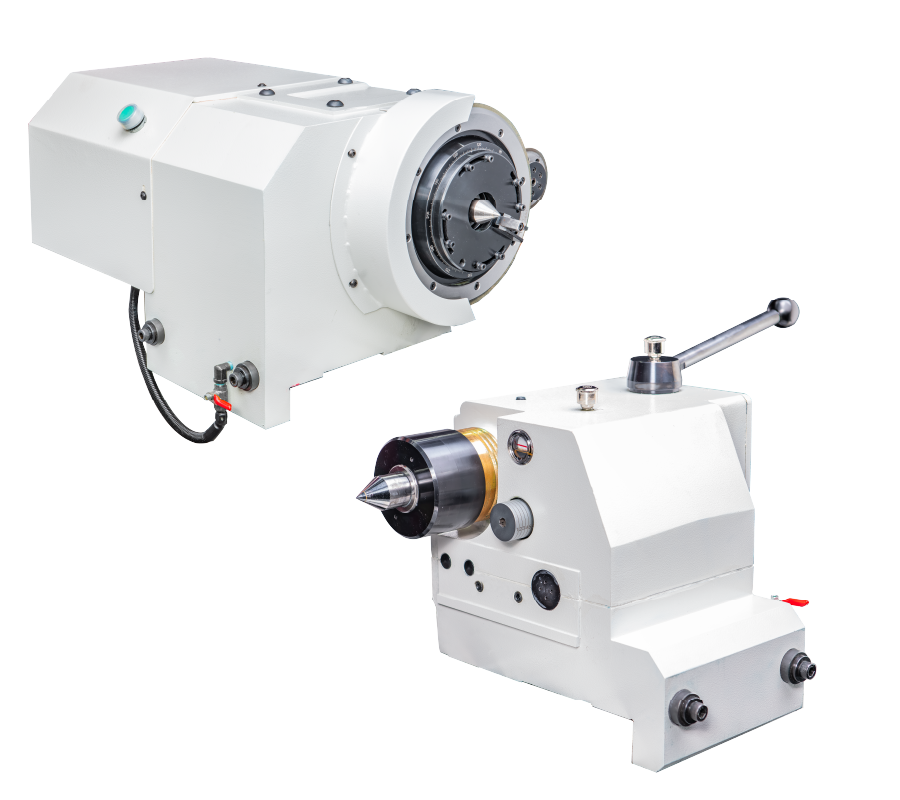
WORK TABLE -C axis precision angle control
■ Working spindle equipped with a Direct Drive motor and precision angle encoder. High resolution of angle tolerance control ±0.2”. Accurate angle control applies for various eccentric, camshaft, crankshaft, and polygon punch grinding.
■ Could do micro-adjustment for taper correction.
FINE ADJUSTMENT TAILSTOCK
■ An auto. oil bath lubrication system has been provided for tailstock to maintain high-level accuracy.
■ The oil level gauge provides a quick check of the oil level.
■ Could adjust enables taper correction in centers fixed grinding way.
G.W. DRESSING
■ Different kinds of dressing devices could be chosen following request.
■ Graph conversation dress setting interface. It's easy to edit dressing parameters.
■ Could choose daimond roller dresser for component and grinding wheel dressing request. (opt.)
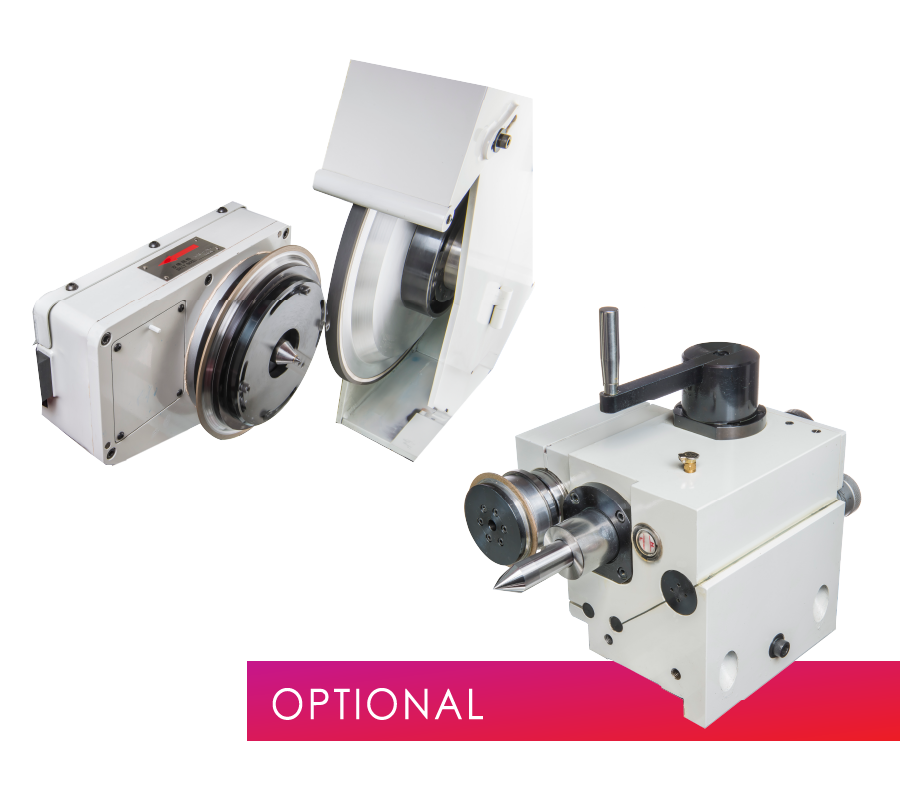
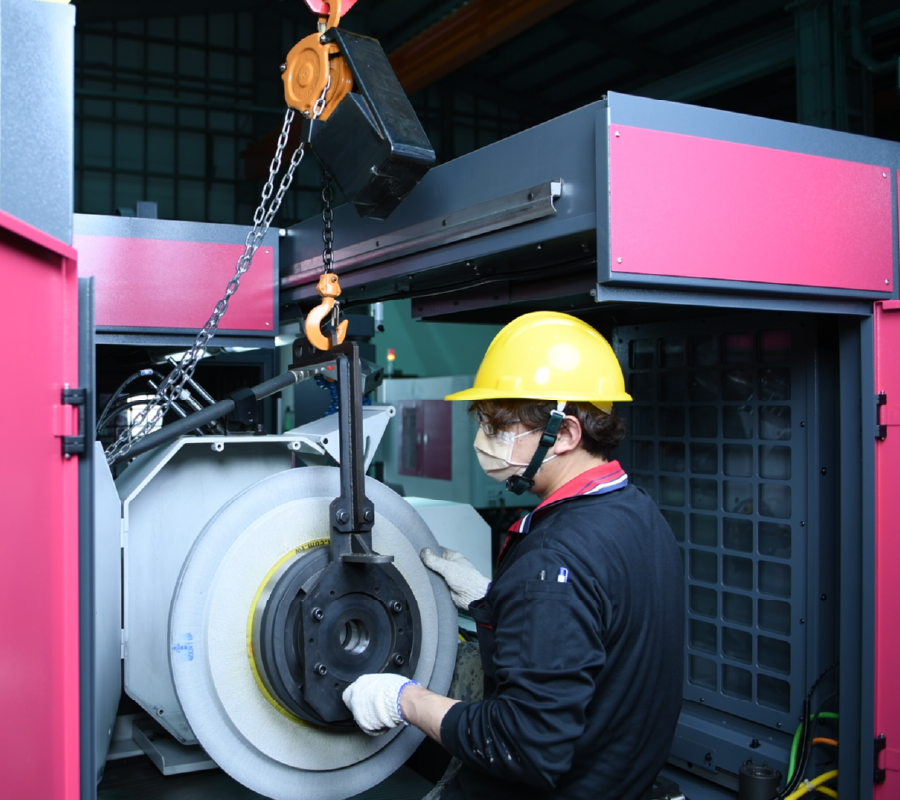
G.W. JIB CRANE
■ Standard equipped with jib crane for loading and unloading grinding wheel. The jib crane base is mounted on the body and covered by a splash guard. Changing the grinding wheel is not affected.
SPECIFICATION
Capacity | |
---|---|
Swing Over Table | Ø370 mm |
Distance Between Centers | 500 mm |
Max. Grinding Diameter | Ø350 mm |
Max. Grinding Length | 500 mm |
Max. Load Held Between Centers | 150 kg |
Center Height (from table to center tip) | 185 mm |
Grinding Wheel | |
Size (O.D. x width x I.D.) | Ø610 x 50 x Ø304.8 mm |
Linear Velocity | 45 m/sec |
Worktable | |
Swiveling Angle | +2° |
Workhead | |
Swiveling Angle | Fixed Type |
Center Tapper | MT. No. 4 |
Spindle Speed | 10 ~ 300 rpm |
Max. Load of Spindle (tool holder included) | 35 kgs (Max. Length: 150 mm) |
Tailstock | |
Center Tapper | MT. No. 4 |
Center Moving | Manual type |
Tailstock Stroke | 25 mm |
Barrel Stroke | ±30 μm |
(opt.) Cylindricity with Micro Adjustment | ±0.03 mm |
X-axis Travel | |
Max. Travel | 300 mm |
Rapid Feedrate Speed | 10000 mm/Min |
Auto. Feeding Speed | 6000 mm/Min |
Min. Feeding Setting | 0.0001 mm |
Z-axis Travel | |
Max. Travel | 750 mm |
Rapid Feedrate Speed | 10000 mm/Min |
Auto. Feeding Speed | 6000 mm/Min |
Min. Feeding Setting | 0.0001 mm |
Drive Motors | |
Grinding Wheel Spindle | 11 kW (Induction motor) |
Workhead Spindle | 2.3 kW (direct drive motor) |
Wheelhead Feed X-axis | 2.01 kW (linear motor) |
Table Feed X-axis | 4 kW (servo motor) |
Lubrication Hydraulic | 0.37kW |
Hydraulic Pump | 0.37kW |
Coolant Pump | 0.75 kW |
Tank Capacities | |
Lubrication Tank (Guideway) | 15 L |
Machine | |
Dimension (LxWxH) | 3000 x 3180 x 2540 mm |
Machine Weight | 8300 kg |
Center Height (from floor to center tip) | 1130 mm |
* The mentioned specifications & dimensions are subject to change without notice.
ACCESSORIES
STANDARD ACCESSORIES
■ CNC Controller (Brand: SEIMENS) x 1set
■ Grinding Wheel and Flange x 1 set
■ Grinding Wheel Inverter x 1 set
■ Diamond Tool Holder ( tailstock mounted type) x 1 set
■ Cooler system for work-spindle servo x 1 set
■ Jib Crane for Loading / Unloading G.W. (for X-35) x 1 set
■ Carbide Tipped Work Centers (2 pcs/set) x 1 set
■ Micro Adjustment Tailstock x 1 set
■ Linear Motor for X-axis x 1 set
■ Linear Scale for X-axis x 1 set
■ Rotary Scale for C-axis x 1 set
■ CAD-CAM Software Graphical Programming x 1 set
■ Electric System x 1 set
■ Fully Enclosed Splash Guard x 1 set
■ Hydraulic System x 1 set
■ Coolant System x 1 set
■ Oil Mist Collector x 1 set
■ Work Lamp x 1 set
■ Tools (Leveling pad) and Tool Box x 1 set
■ Cam-locked Driving Dogs
■ Work Holder (2pcs/set)
■ 2-point Steady Rest
■ Adjustable 3-jaw Scroll Chuck
■ Adjustable 4-jaw Scroll Chuck
■ Diamond roller dressing device (connecting with workhead by flange)
■ Diamond roller dressing device (tailstoke mounted type)
■ Hydraulic Tailstock
■ Wheel Balancing Stand and Arbor
■ Auto. Grinding Wheel Balancer
■ Spare Grinding and Wheel Flange
■ Touch Probe Gauge
■ Gap Control
■ Customized Workpiece Drive Fixture
■ Magnetic Coolant Separator
■ Paper Filter