angular type G.W. | X-P series
X-3550P
plunge grindingINTRODUCTION
The TOPKING X-P series CNC External Cylindrical Grinder boasts unique features, incorporating plunge grinding and an angular wheelhead to showcase exceptional end-face grinding performance. It seamlessly conducts both end-face and outer diameter grinding, equipped with a 180mm wide grinding wheel for efficient one-time processing, significantly enhancing production efficiency.This series features a reinforced structure, a heavy-duty main spindle, and a tailstock to ensure robust support. The cross-slide design of the X and Z axes aids in minimizing the footprint and axial travel, further elevating the overall efficiency of the machine tool, providing customers with the most suitable and reliable grinding solutions.
| CAPACITY
Swivel Over Table: Ø350 mm
Distance Between Center: 650 mm
Max. Grinding Dia.: Ø350 mm
Max. Grinding Length: 500 mm
MACHINE FEATURE
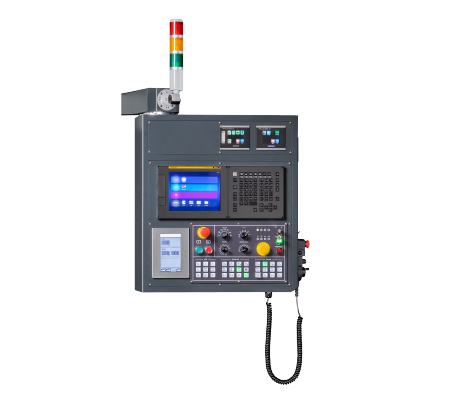
USER FRIENDLY OPERATION SYSTEM
The built-in advanced CNC control system is equipped with GUI. The operator can divide the complex workpiece into several grinding processes through the guidance of the graphic, and simplify the process editing of grinding and dressing in a numerical way.No complicated programming (G code, M code) is required, and the most convenient operating environment is provided.
RIGID MACHINE BASE
■ High rigidity machine base made of Meehanite cast iron through annealing and aging treatment.
■ Slideway though high-frequency hardening and precision grinding process. Machine base with stable material and strengthen construction for deformation-free and outstanding wear resistance.
■ The machine’s structure is different from the light weight design philosophy in the past; it substantially consolidates the rigidity of body and parts structure, takes being more stable as the appeal, and adopts thick and solid sliding seat mechanism, slide way 1 V 1 flat structure providing the best precision and stability of moving when doing grinding.
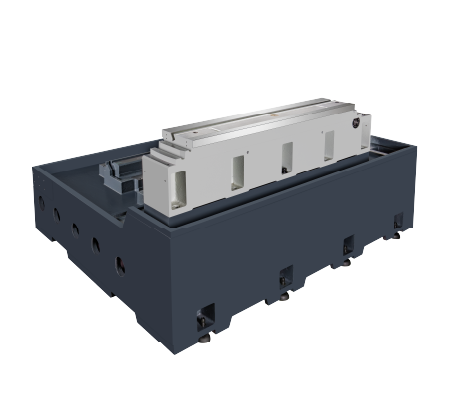
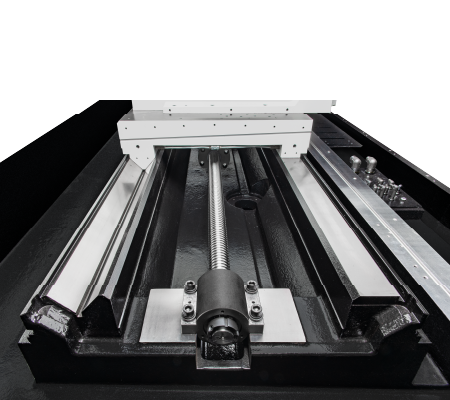
HIGH RIGIDITY SLIDEWAY
■ The guideway features a 1V1 flat design, undergoing high-frequency hardening treatment and precision grinding, substantially improving the wear resistance and stability of the guideway. High-frequency hardening treatment effectively increases the material's surface hardness, and precision grinding further ensures surface smoothness, providing optimal accuracy throughout the entire grinding process.■ Employing a dual-axis system with high-rigidity box way sliders and large-sized ball screws, not only enhances the load-bearing capacity but also ensures the wheel head's stable and smooth movement throughout the operation.
WORK TABLE
The worktable is consistently anchored to the base, featuring a cross-slide design for the X and Z axes, minimizing travel and improving processing speed and stability.
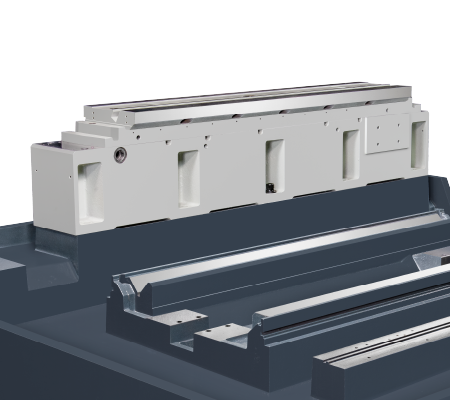
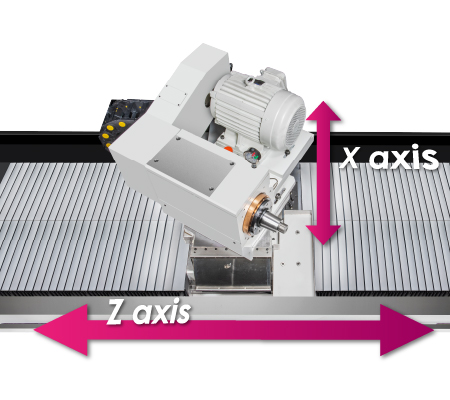
CROSS-SLIDER DESIGN & AXIS GUIDANCE
■ The X and Z axes are designed with a cross-slide structure, allowing for flexible operations and effectively reducing the overall footprint.
■ Featuring a dual-axis design with fully enclosed telescopic guards, this configuration ensures comprehensive protection for the transmission structure. It effectively isolates grinding debris and prevents coolant contamination, guaranteeing long-term and stable machine operation.
WHEELHEAD CONSTRUCTION
■ Bearing type of G.W. spindle adopts precision bearings, which has a long service life and is relatively easy to replace, repair and maintain.
■ The G.W. spindle is made of high-quality alloy steel SNCM-220, which has undergone multiple treatments such as normalization, quenching and tempering, carburizing heat treatment, and cryogenic treatment. Afterwards, precision grinding and mirror treatment are carried out, and the surface hardness reaches above HRC62°. Guarantee no deformation, wear resistance, high precision forever.
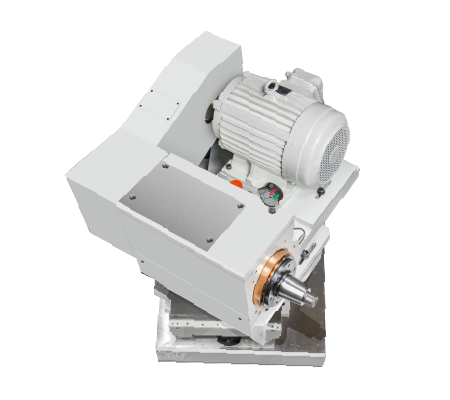
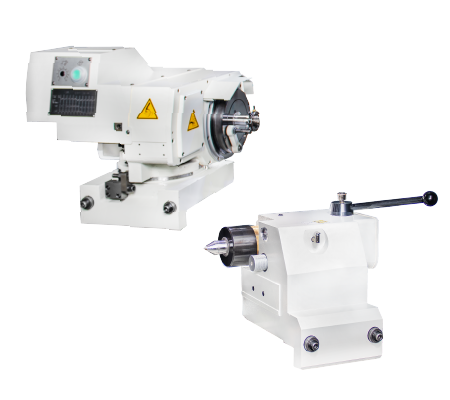
RIGID WORKHEAD AND TAILSTOCK
■ The workhead and tailstock are specifically designed to accommodate heavy workpieces, providing solid structural rigidity to enhance the overall load capacity.
■ The workhead is driven by a servo motor, allowing for step-less variable speed adjustment to provide a more flexible operational experience.
■ Hydraulic tailstock (optional) with a supporting device for convenient operation.
■ The workhead and tailstock feature a flat air pressure design, allowing for effortless operation, minimizing friction during movement, and thereby extending the overall equipment lifespan.
■ Both the workhead and tailstock feature a cooling system for the center hole, preventing deformation from frictional heat.
DIAMOND TOOL HOLDER MOUNTED ON TAILSTOCK
(STANDARD FOR X-P SERIES)
■ Dressing device is fixed on the tailstock.
■ Diversified diamond tool holder types can be selected according to the workpiece requirements.
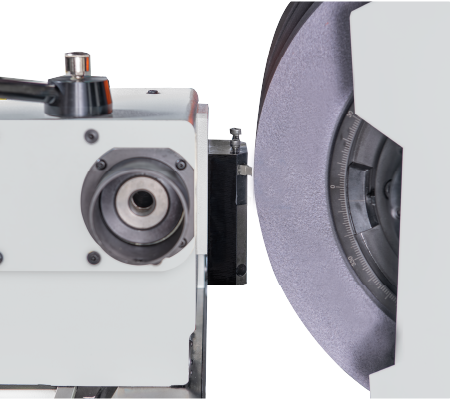
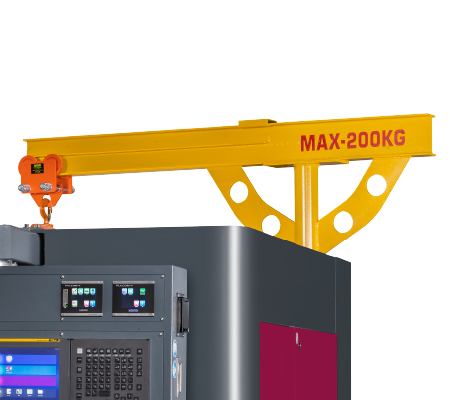
G.W. JIB CRANE
(STANDARD FOR X-35 SERIES)
The X-35 series features an integrated jib crane for wheel replacement, installed within a full splash guard. This space-saving design maximizes flexibility, allowing wheel replacement without constraints from working space or equipment. It offers convenience while ensuring a safe replacement operation.GRINDING CYCLE
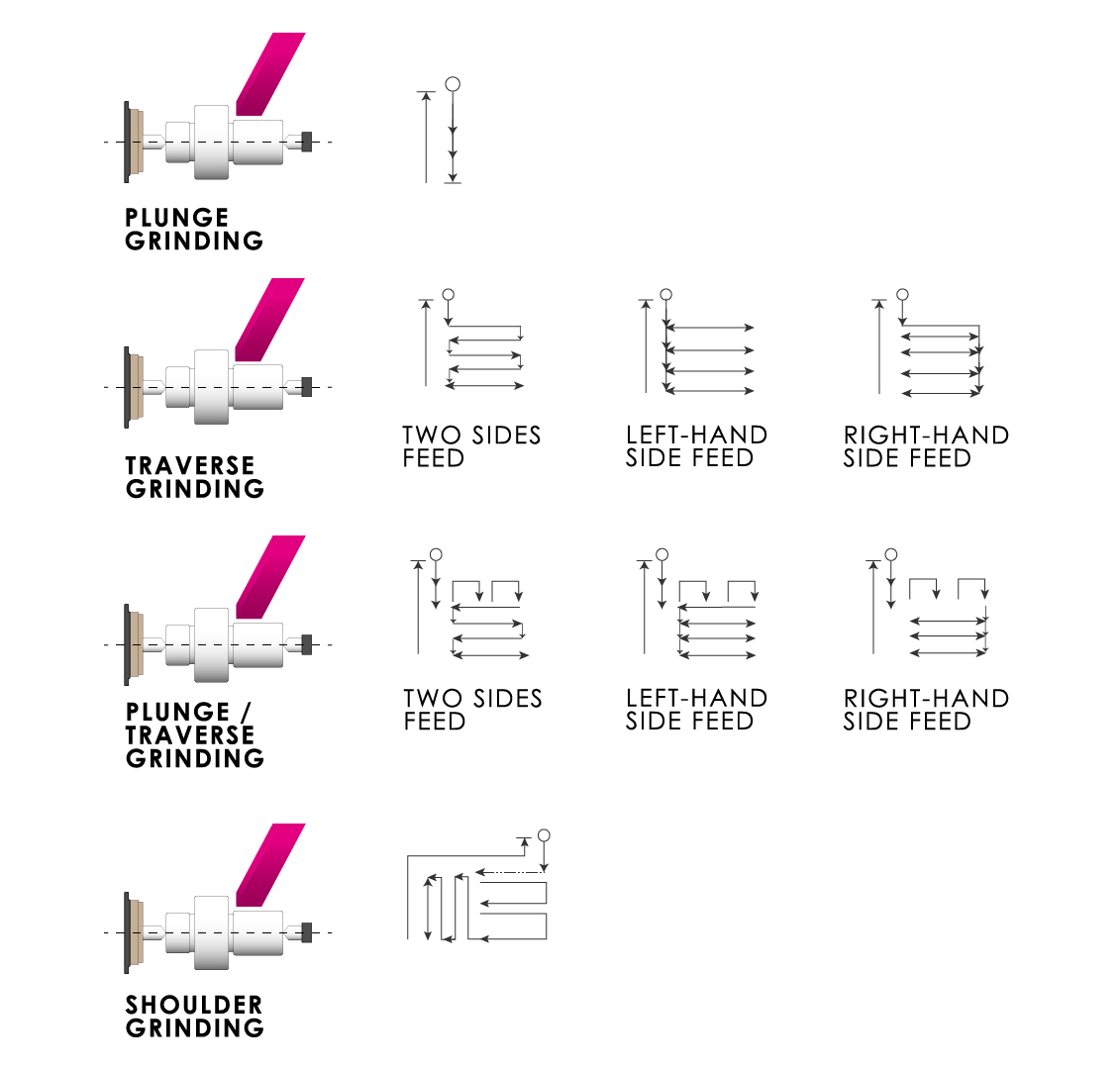
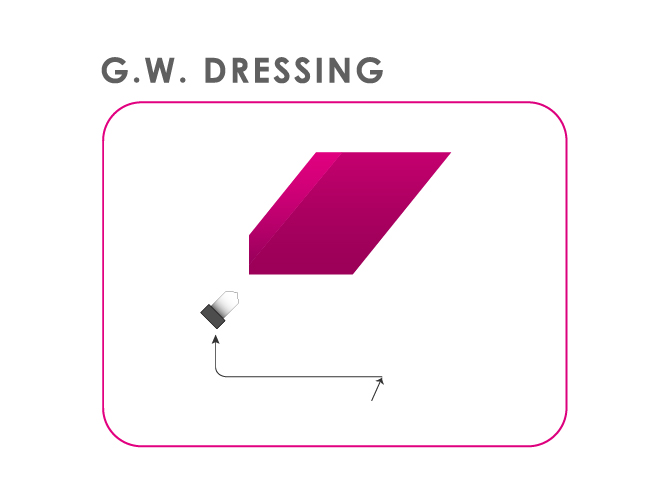
SPECIFICATION
Capacity | |
---|---|
Swing Over Table | Ø350 mm |
Distance Between Centers | 650 mm |
Max. Grinding Diameter | Ø350 mm |
Max. Grinding Length | 500 mm |
Max. Load Held Between Centers | 150 kg |
Center Height (from table to center tip) | 185 mm |
Grinding Wheel | |
Size (O.D. x Width x I.D.) | Ø610 x 50(opt.:180) x Ø203.2 mm |
Linear Velocity | 45 m/sec |
Worktable | |
Swiveling Angle | 0° ~ 3° |
Workhead | |
Swiveling Angle | Fixed Type |
Center Tapper | MT. No. 4 |
Spindle Speed | 10 ~ 300 rpm |
Max. Load of Spindle (tool holder included) | 35 kgs (Max. Length: 150 mm) |
Tailstock | |
Center Tapper | MT. No. 4 |
Center Moving | Manual type |
Tailstock Stroke | 25 mm |
X-axis Travel | |
Max. Travel | 270 mm |
Rapid Feedrate Speed | 6000 mm/Min |
Auto. Feeding Speed | 0.001 ~ 2000 mm/Min |
Min. Feeding Setting | 0.001 mm |
Z-axis Travel | |
Max. Travel | 800 mm |
Rapid Feedrate Speed | 6000 mm/Min |
Auto. Feeding Speed | 0.001 ~ 2000 mm/Min |
Min. Feeding Setting | 0.001 mm |
Drive Motors | |
Grinding Wheel Spindle | 11 kW |
Workhead Spindle Motor (servo motor) | 1.8 kW |
Wheelhead Feed X-axis (servo motor) | 1.5 kW(MITSUBISHI) / 1.4kW(FANUC) |
Table Feed X-axis (servo motor) | 3.5 kW(MITSUBISHI) / 4.4kW(FANUC) |
Lubrication Hydraulic Motor | 0.37 kW |
Hydraulic Pump | 0.37 kW |
Coolant Pump | 0.18 kW |
Tank Capacities | |
Lubrication Tank (Guideway) | 30 L |
Lubrication Tank (Optional) | 30 L |
Coolant Tank | 30 L |
Machine | |
Dimension | 3477 x 3033 x 2541 mm |
Net Weight | 8000 kg |
Center Height (from floor to center tip) | 1250 mm |
* The mentioned specifications & dimensions are subject to change without notice.
ACCESSORIES
STANDARD ACCESSORIES
■ CNC Controller (Brand: Mitsubishi) x 1set
■ Grinding Wheel and Flange x 1 set
■ Carbide Tipped Work Centers (2 pcs/set) x 1 set
■ Diamond Tool Holder ( tailstock mounted type) x 1 set
■ Jib Crane for Loading / Unloading G.W. x 1 set
■ Linear Scale for X-axis x 1 set
■ Grinding Wheel Inverter x 1 set
■ Electric System x 1 set
■ Fully Enclosed Splash Guard x 1 set
■ Hydraulic System x 1 set
■ Coolant System x 1 set
■ Work Lamp x 1 set
■ Tools (Leveling pad) and Tool Box x 1 set
■ Hydraulic Tailstock
■ Cam-locked Driving Dogs
■ Work Holder 2 pcs/set
■ 2-point Steady Rest
■ Adjustable 3-point Steady Rest
■ Adjustable 3-jaw Scroll Chuck
■ Adjustable 4-jaw Scroll Chuck
■ Wheel Balancing Stand and Arbor
■ Auto. Grinding Wheel Balancer
■ Spare Grinding Wheel and Flange
■ Diamond Roller Dressing Device (worktable mounted type)
■ Diamond Roller Dressing Device (tailstock mounted type)
■ Touch Probe Gauge
■ Auto. In-Process Gauge
■ Gap Control
■ Linear Scale for Z-axis
■ Magnetic Coolant Separator
■ Paper Filter
■ Oil Mist Collector